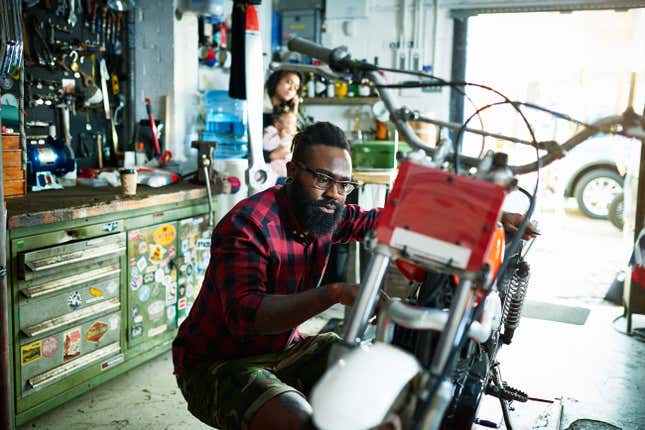
I asked for your best project bike or car tips to help kickstart my CB350 project back to life and you delivered. Whether it’s staying organized or going the extra mile with research, you all seem to know your way around a project or two.
I asked for your best project bike or car tips to help kickstart my CB350 project back to life and you delivered. Whether it’s staying organized or going the extra mile with research, you all seem to know your way around a project or two.
You said you are already past the disassembly phase, but there are two things I thank my past self the most for.
Photograph everything. Every stage of disassembly. How this thing connected to that thing. The orientation of that doohickey. Digital photos and an ever-present smartphone make this oh so easy.
Bag and label all fasteners. Draw diagrams of where different length bolts go if you need to. Plastic bags and 3x5 cards are cheaper than losing your sanity later.
Submitted by blue72
Don’t buy a project from the rust belt (aka my Miata from Ohio).
Submitted by Midlife Miata Driver
Research the crap out of whatever it is you’re going to disassemble that day. I find that one video or forum post usually isn’t enough. I just replaced the oil cooler in my van. The first video I watched showed that the fuel rails had to be removed. The second one showed that they didn’t, and also that the clips for the injector connectors tended to stick and it was ok to pry on them a bit.
Submitted by dbeach84
Don’t buy a project to drive. If you want to drive a classic, then buy a runner. You buy a project to wrench on, and maybe one day it’ll be finished. Don’t buy and think you’ll be driving it though, because chances are the day you sell it it’ll be to be someone else’s project.
Submitted by skeffles
Take super meticulous notes on everything you touch, especially electrical. I stripped down my Fiat 500 to the bones, and removed 3 shopping bags full of factory wire harnesses, and was real careful about writing down absolutely everything I could. Also while modifying some circuits, it helped to know in advance because of other notes I took, which wires went where. The multimeter is your friend!
Record a video of you working on it so you can watch it back later in case you ever lose track of how something fit.
Draw a simple diagram on a piece of cardboard of things you’re taking apart, and stick the screws through the cardboard in the spot you took them off of, so you know where they came from. Or just lightly screw them into the hole you removed them from after you take the thing off. Also helps to make a colored mark on the screw and the screw hole.
Submitted by StalePhish
Lots of projects/restorations require a LOT of upfront work before you can actually use the thing you’re working on. That’s the nature of the beast. But for motivation and making it doable/sustainable (and not become “that guy” who ends up listing their project on Craigslist along the lines of “just get it out of my shop, or my wife is going to kill/divorce me”), try to have little success milestones along the way. As in, do the minimal thing you have to do to get it “working” in some way, even if just for a mini ride in the back yard. And celebrate each and everyone of those successes, and share them with friends and your loved ones, so they get what you’re doing and why.
Submitted by G42Dog
Get a JIS screwdriver set. $18 from Amazon. See all those cross-head screws with a dot in one corner? A Philips screwdriver will slip and cam out, but a JIS screwdriver will lock in.
Submitted by Gubbin
Join a local car club or even a Facebook or Reddit group specific to your model vehicle for advice on your project and to source parts.
I hate FB with a passion, but I joined the Buick Wildcat group and was able to source an aluminum power steering pump bracket from a fellow Wildcat owner in Baker City OR from the comfort of my bedroom in Metro Atlanta.
Another member was able to steer me in the right direction for a reproduction front grill badge.
Obviously you have to be wary of scammers and bad advise, but the collective knowledge and experience of these groups is invaluable and will save you a ton of time and frustration.
Submitted by Earthbound Misfit I
Have a plan, outline what you plan to do, how you plan to do it and identify dependencies and bottlenecks like parts availability or outside suppliers (body shop, machine shop, plater)player. Then follow and track the plan, whiteboard, Kanban wall whatever it takes to keep you moving forward
Submitted by Slow Joe Crow
1. Swap your switches from power to ground. Don’t put amperage load on your switches, even if they’re rated for it. That includes triggers for relays: just send the ground side to the bulkhead terminator, not the power. The power can come straight from a battery positive bus strip.
2. For cars with digital components, use separate ’dirty’ and ‘clean’ power and ground bus. Those digital components like ECUs etc don’t like noise from fan motors, fuel pumps, water pumps, etc. They also don’t like power spikes from relays and solenoids turning on and off. If you have an HEI distributor or a high power digital ignition unit on a carbureted car, probably a good idea to isolate that power and ground wise.
3. Use ground bus strips connected directly to the battery negative (sad) side for grounds. Don’t ground everything to the body. That sucks. This also goes with #1. If you are running power to your switches and just grounding things to the body... yeah it works but does it work?
4. Avoid damaging sensitive stuff with power spikes by putting a diode across the positive and ground. This is called a ‘flyback diode’ and it’s a good idea to keep voltage spikes from burning out components. Most modern electronics will have internal diodes, but still, its not expensive and it’s better-er.
5. Use a good bulkhead connector. Don’t just put wires through holes in the firewall.
Submitted by Brian Madigan