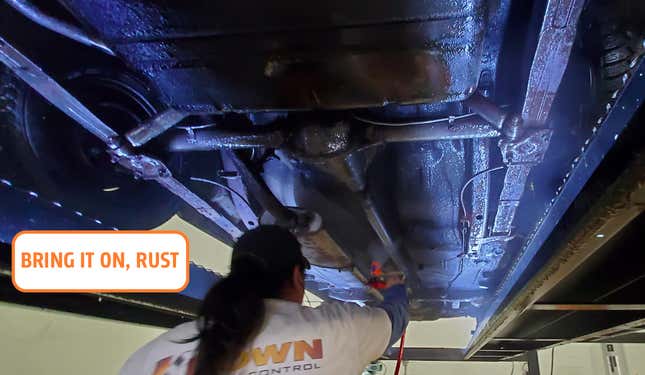
In the halls of Chrysler, old-timers used to talk about a rust-proofing shop across the bridge in Canada. “Yeah, they use oil, which isn’t allowed in the U.S.,” they would say before highly recommending the treatment to preserve old cars. Now that shop is in the U.S., and I just checked it out; here’s how a company called Krown rust-proofed my 1965 Plymouth Valiant.
I actually don’t know if Krown was illegal in the U.S. at any point, but that’s the rumor that swirled around the halls of Fiat Chrysler, and it’s what the manager of the Rochester Hills, Michigan Krown location confirmed to me yesterday. He said laws relating to petroleum-based undercoating became more accommodating in recent years, allowing Krown to make its way stateside. Again, I’m not sure if this is actually true, but that’s not important for this article; what’s important is whether this stuff actually prevents cars from rusting. Update: I spoke with Krown’s Vice President, Jeremy Young, who told me that Krown was never illegal in the U.S. This appears to just be a rumor.
It’ll be a while before I can give the before and after assessment needed to answer that question, so I’ll just tell you what happened when I took my 1965 Plymouth Valiant to my local Krown shop, because it’s quite interesting. The process involves a lot more than just spraying fluid onto an undercarriage.
First, What Is Krown?
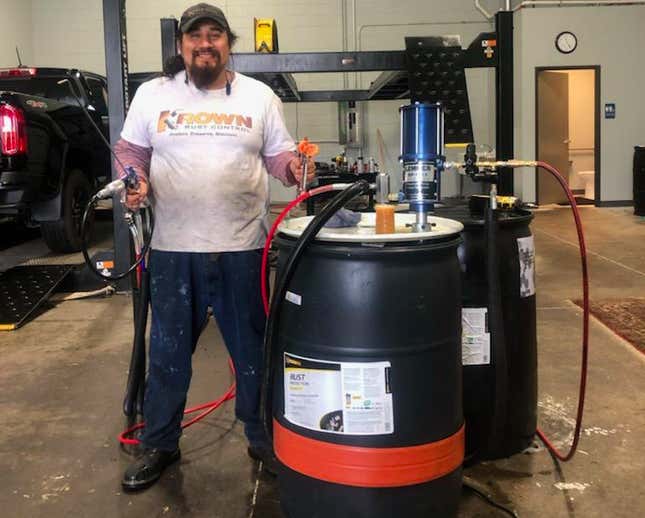
First, a quick look at what this fluid actually is. I don’t know a ton about it, but I can tell you that it is amber and has the consistency of maple syrup (you can see a container of the fluid below). It’s petroleum based, and Krown applies it to cars by heating it up to 135 to 150 degrees Fahrenheit, pressurizing it to about 95 psi, and then spraying the atomized oil onto and into the car. “It creates a fog that literally coats everything,” Rochester Hills Krown owner John Hart told me over the phone.
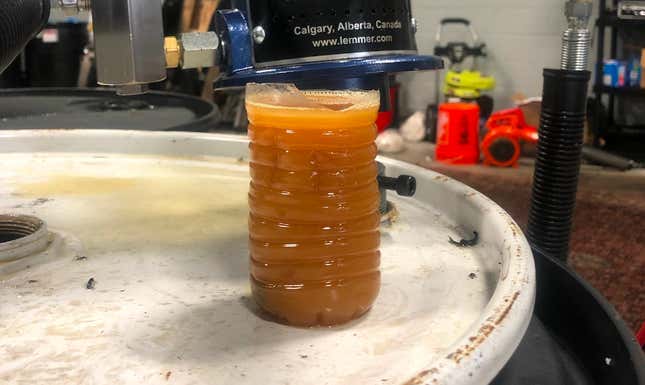
As the fluid cools on the surface, it thickens. On its website, Krown describes some of its product’s properties, writing:
Krown ... is self-healing and is constantly creeping, remaining active to continuously repel moisture and keep it away from the metal surface. In addition, unlike coating-type products, Krown penetrates into even the tightest seams and spot welds delivering a much more effective and comprehensive protection. One final difference is the added benefit that Krown offers of lubricating many moving parts on a vehicle such as door locks, brake cables, power antennas, etc. Coating products cannot do this.
The company also claims that its treatment is environmentally friendly, non-flammable, and nontoxic. Krown recommends that car owners have their vehicles treated annually.
I should mention that Krown isn’t the only rust-proofing company out there; Ziebart, headquartered right up the street from me in Troy, MI, also has an excellent reputation. The exact differences between various underbody treatments — wax-based versus tar-based versus oil-based, and the different application methods — is something I’ll get into in a future article. I just chose Krown because of its reputation in Michigan and Canada, the salty birthplace of the company established in 1986.
Krown Drills Holes Into The Car To Protect It From The Inside
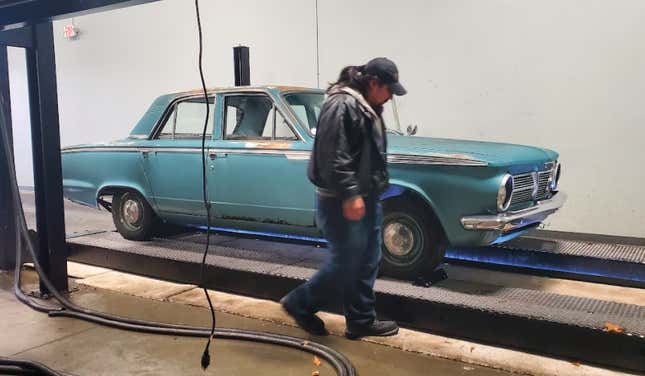
The first thing I did when I arrived at the Krown facility in Rochester Hills, Michigan was drive onto a ramp, which normally wouldn’t be worth mentioning except that it was a difficult endeavor due to how much oil was on the ground. My Valiant’s rear tires just couldn’t grip the smooth, fluid-covered garage floor located in the suburban Michigan business park, so I had to take a bit of a run-up.
Once aboard the hoist, an extremely enthusiastic manager named George began drilling holes into my car. This optional step in the rust protection process allows Krown to spray its petroleum-based fluid into the body, protecting doors and rocker panels that might rust from the inside (rusting from the inside is very common, as many closures aren’t truly sealed from the elements, and tend to trap moisture-holding debris).
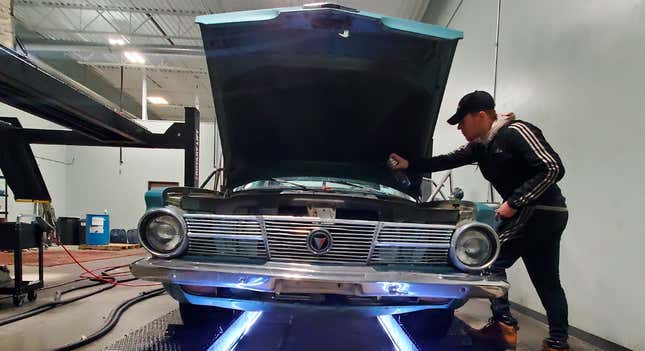
While George was drilling holes, his assistant Aiden sprayed silicone onto the rubber seals in the door jambs and under the hood and trunk lid. Krown’s fluid has a tendency to swell and damage rubber seals; the company applies silicone to prevent this.
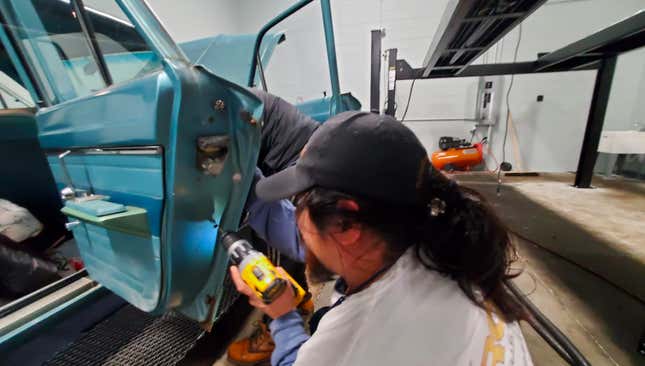
George drilled holes in a number of locations, all of which were hidden from view. In the image above, he’s drilling a hole into the rear passenger’s-side door to later coat its interior surfaces with a film of oil.
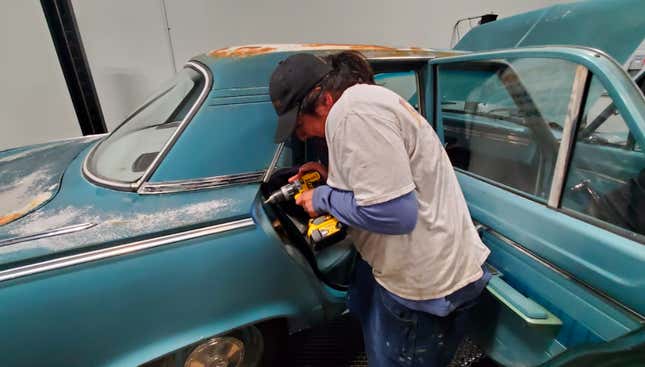
The image above shows George drilling into the rear quarter panel via the door jamb.
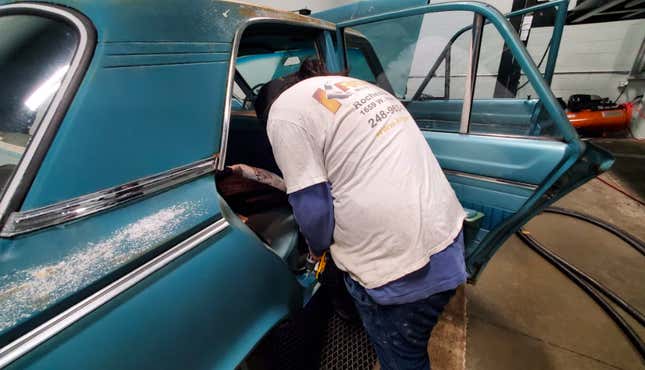
Above you can see George drilling into my rocker panel from the top, also in the door jamb.
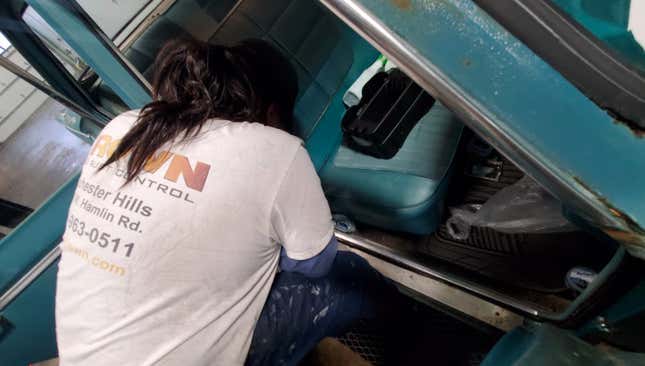
He drilled the holes at the front of the rocker panels as well via the front door jambs.
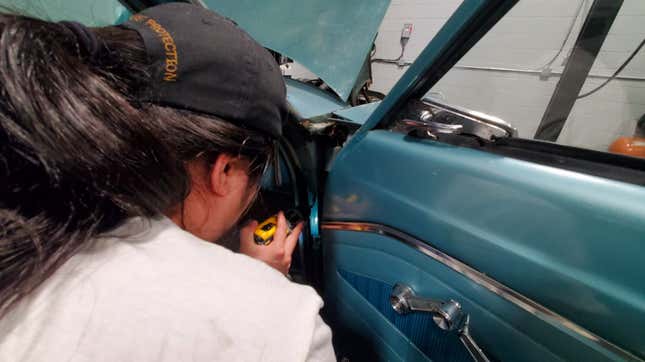
Plus George drilled into the vertical unibody structure that supports the front door hinges; his goal with all this was to make sure that every void in the body that could possibly hold dirt/moisture had its surfaces coated in oil.
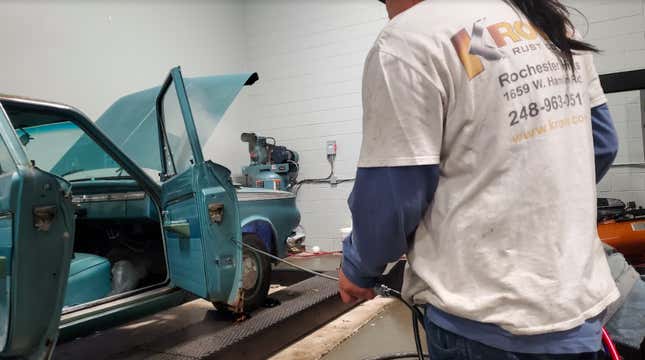
With holes drilled, George inserted a long metal wand. One end of the wand had a fitting for a hose being fed high-pressure, pre-heated oil via an oil tank attached to an air compressor. The other end of the wand, shown inserted into my door in the image above, has a spray nozzle that shoots oil perpendicular to the wand’s axis. This allows George to coat all surfaces in the void by rotate the wand as he pushes and pulls it into and out of the orifice.
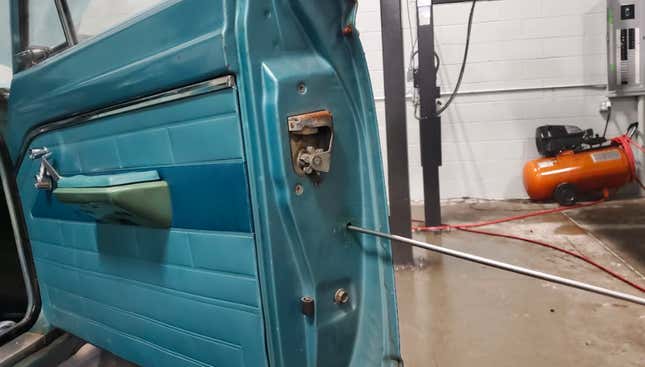
Here’s a look at George’s technique for injecting oil into doors:
He repeated the process in my other doors, in the rocker panels, and even in my hood and trunk lid.
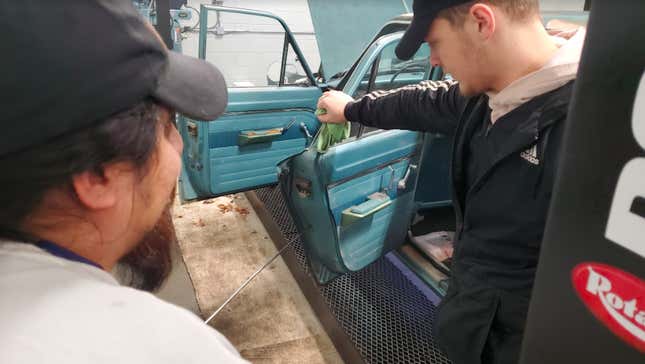
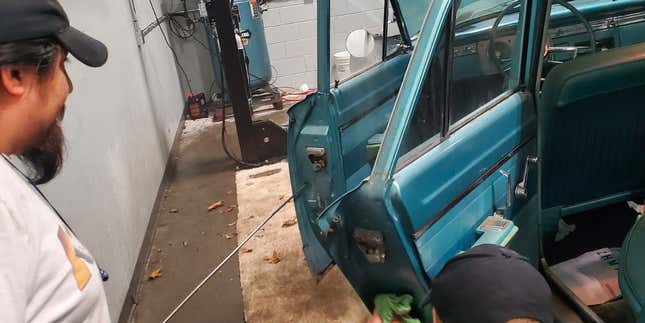
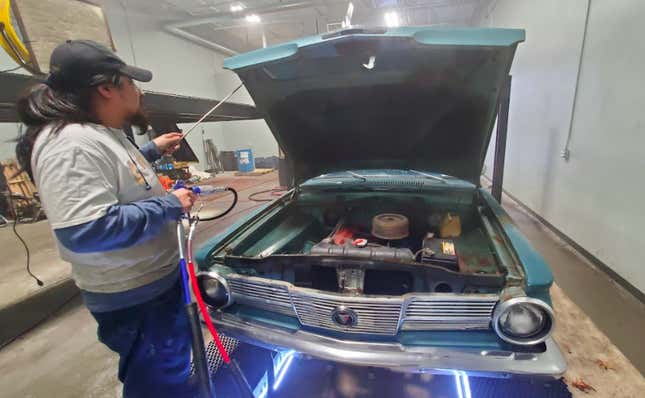
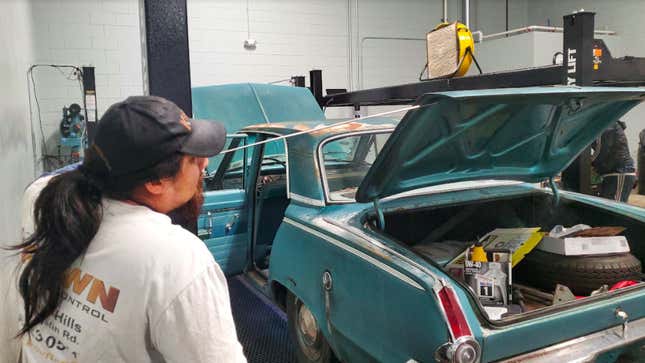
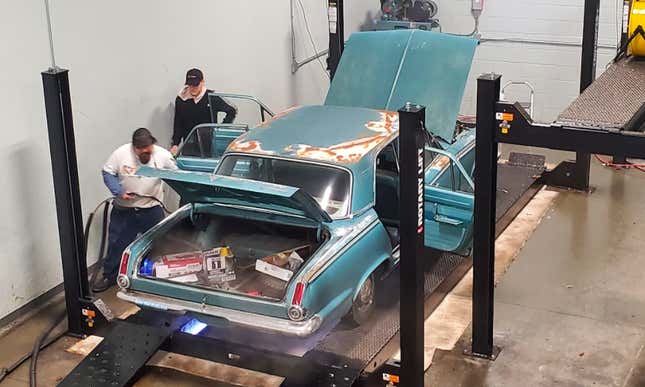
He also used the wand to spray certain cracks/seams in the unibody, as well as to lubricate hinges and latches, for good measure.
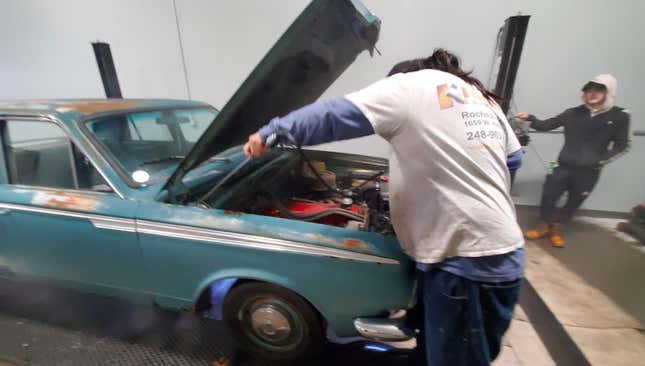
By the time George was done filling up my vehicle’s doors with hot atomized oil, they were dripping (you can see the white oil on the door’s bottom seam):
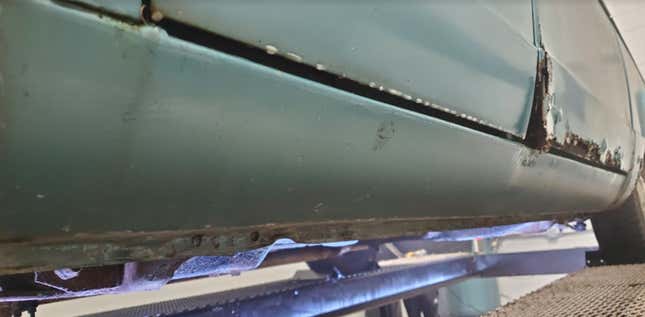
Aiden greased up all the holes to prevent the cut sheetmetal from rusting, and to lubricate them to more easily take the plugs meant to keep dirt and moisture from entering:
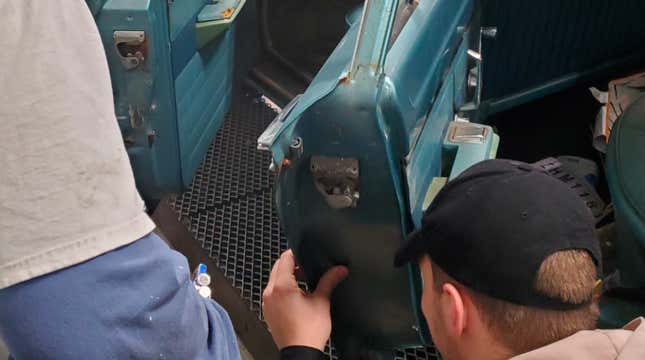
Here’s a closer look at the rubber plugs that Krown installed into the holes that George drilled into my Valiant’s body:
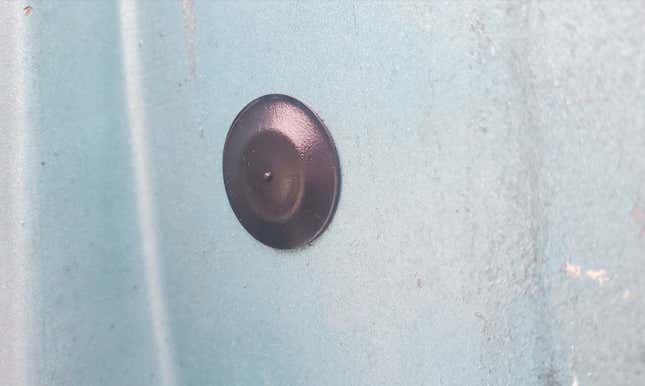

With my 1965 sedan’s body injected with oil, it was time to raise the vehicle on the hoist.
Spraying Inside The Frame And All Over The Underbody
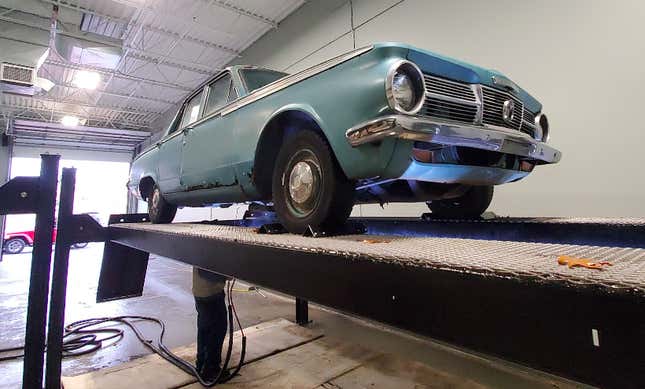
With the car in the air, it was time for one last job for the wand. George shoved the thing into the holes in the main unibody rails.
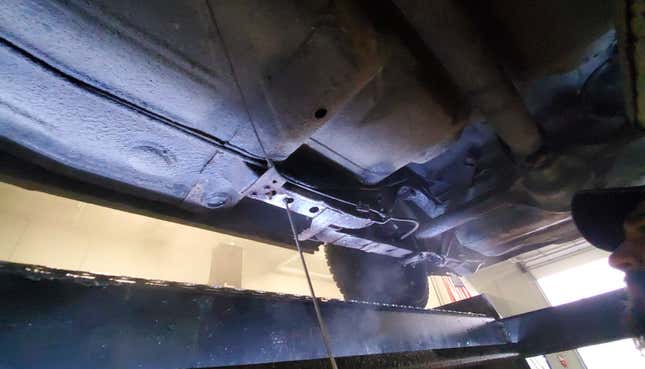
I watched as hot oil mist (which John, the owner, refers to as “fog”) shot out of the other holes in the rails, indicating that the oil was coating all of the inner walls.
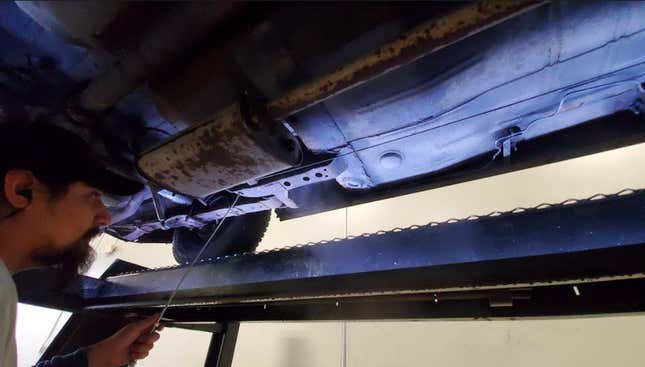
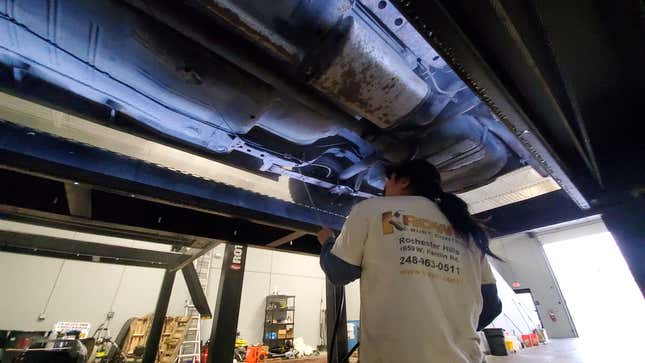
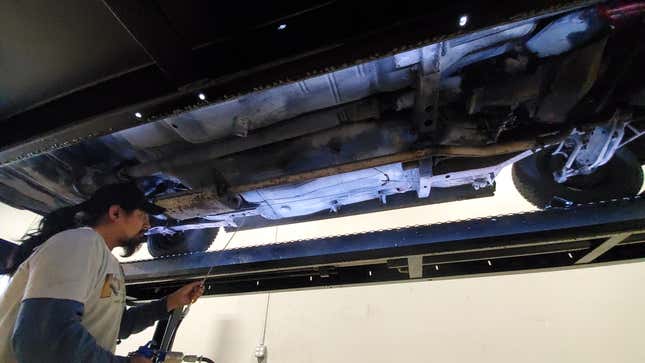
For the underside of the car, George used a slightly different wand. Here’s a look at George’s wand selection, in case you’re curious:
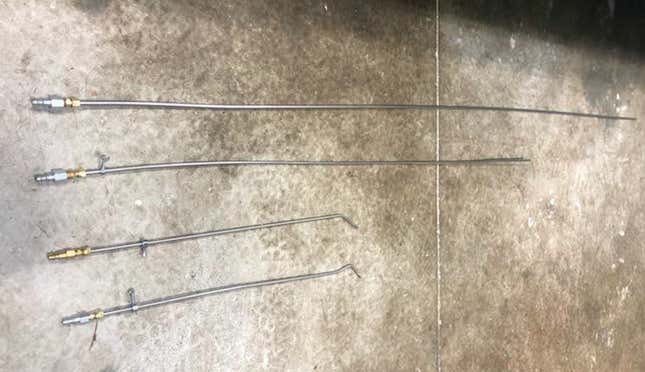
You can see that, unlike the wand shown in the video above, this one has a slight bend:
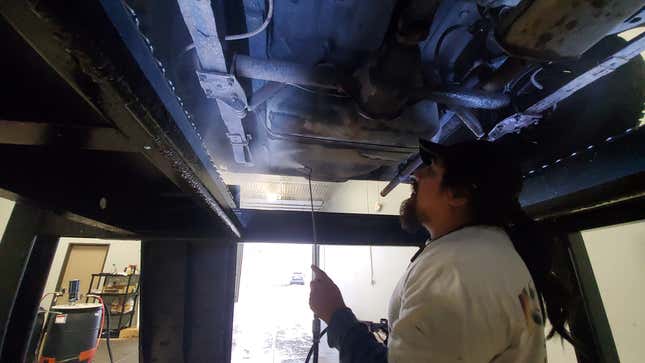
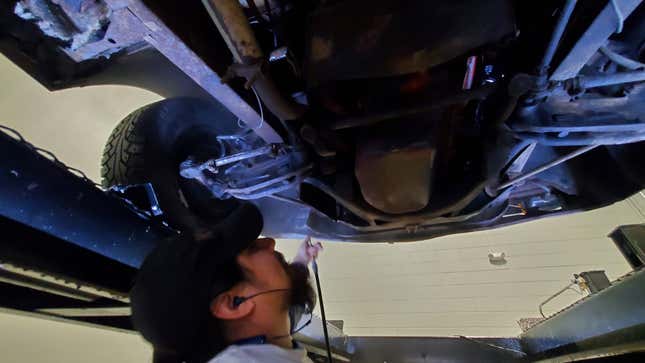
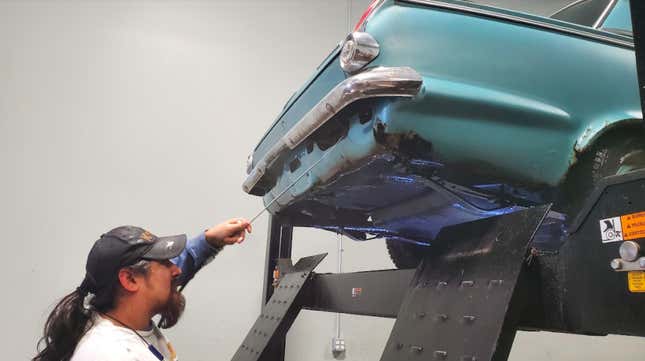
In addition to filling the main unibody rails, George used that wand to coat underbody surfaces that couldn’t otherwise be reached with a lower precision, higher-volume sprayer (which I’ll show in a moment).
Here’s a short clip of George using the wand underneath my Valiant to fill the rails and to coat other hard-to-reach areas with oil:
Next, it was time for George to hit my Valiant with serious volumes of hot oil.
The High-Volume Sprayer
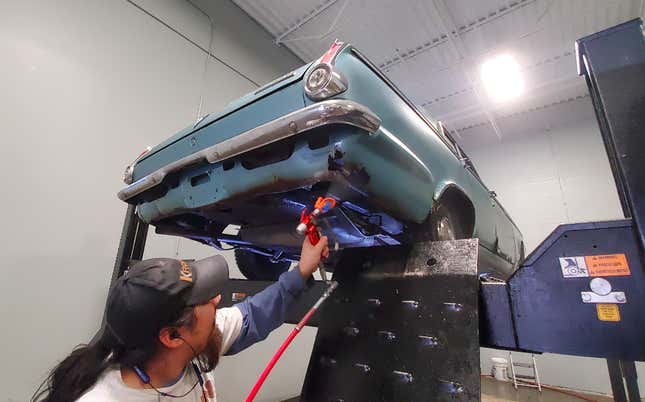
The next tool that George reached for was a high-volume sprayer, which he referred to as, simply “overspray.” This gun shoots ridiculous amounts of atomized oil in a flat pattern, making it easy to cover large surfaces. George began by coating the lower parts of the car’s exterior — the rocker panels, rear quarter panels, front fenders, and front and rear lower fascias — with goo. Then he stepped underneath.
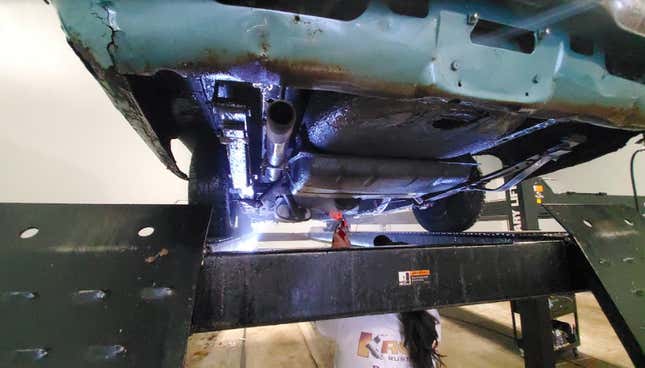
For the next fifteen minutes, George attacked the underside of my Valiant with copious quantities of rust-inhibiting fluid. I stood in amazement as he held that trigger, oil dripping onto his head, and hopefully not coating his lungs:
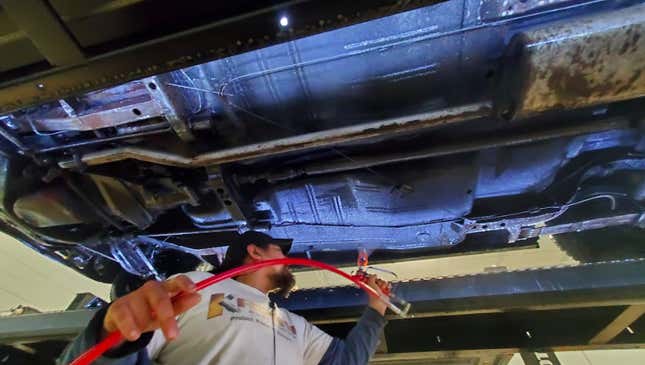
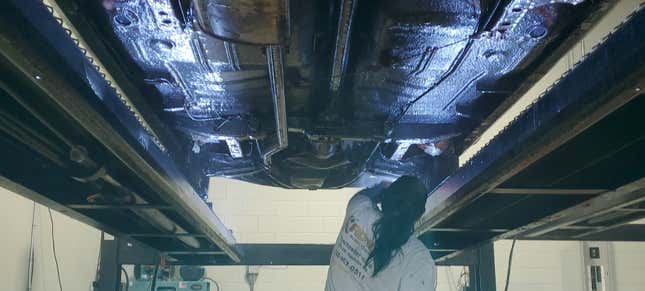

Here’s a clip of George going to town on my Valiant’s underbody with that high-volume oil sprayer:
With the underbody coated in oil, George lowered the vehicle and hit my wheel wells with oil. This is an important area to coat, since it’s where the tires kick up dirt and salt, which accelerate corrosion:
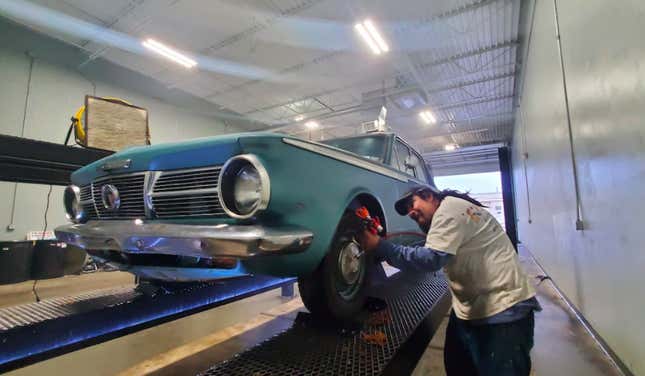
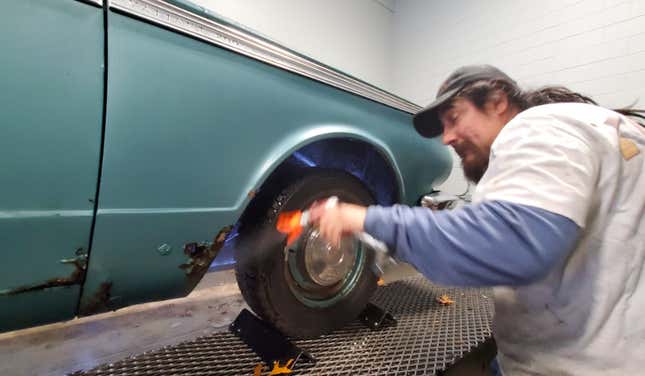
That was pretty much the whole job. From drilling to wanding to overspraying, the whole operation took about an hour and cost me $130 (with coupon; typically it’d cost about $150 depending on the car).
Aiden cleaned the oil fog from my windows before I hit the road, where — for a few minutes — I did smell a bit of oil emanating from my hot exhaust. I arrived at my house, I chose to park in my backyard, since Krown says I should expect the fluid to drip for a couple of days, and I don’t want to sully my landlord’s driveway. Of course, here’s what happened when I tried parking in my backyard:
It’s going to be a long winter. But hopefully not a rusty one. I’ll keep you posted.
Update (December 7, 2021 1:55 P.M. ET): This story has been updated to include notes from my discussion with Krown’s vice president, who responded to my inquiry after Jalopnik initially published this story.