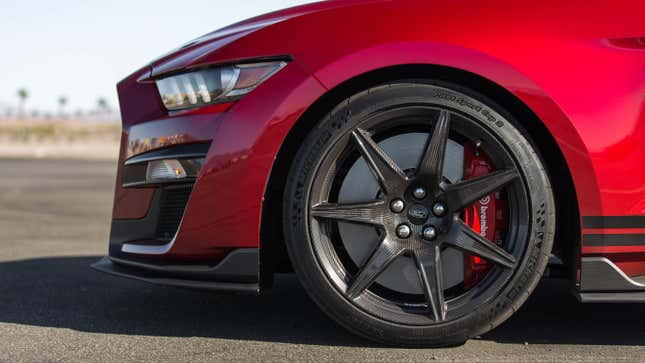
The new 760 horsepower 2020 Ford Mustang Shelby GT500 is an impressively long-named machine. But as production cars hit levels of power previously considered unreachable, we are coming to a point of diminishing returns. Our ability to create titanic power is outstripping our ability to put said power to the ground without massive amounts of electronic intervention. Intervention, which by its very nature, reduces power in order to maintain traction.
So if increasing power comes with caveats like that, where can we look to next in our never-ending quest to go faster? Well, to paraphrase the great Colin Chapman, you start by adding lightness. And on the GT500, we can look to the carbon fiber wheels as a great example of that.
(Full Disclosure: Carbon Revolution wanted me to check out its updated production facility so bad that it stuck me on an 18-hour flight to Australia and didn’t once offer me any shrimp on the barbie over the three days I was there. I did get see a koala, though. So I’ve got that going for me.)
My first encounter with carbon wheel manufacturer Carbon Revolution was at the Mustang GT350R launch a few years back. As taken as I was with the supplier’s wheels and the tech behind them, I was so focused on driving the GT350R that I didn’t give these wheels their due when I wrote the review of the car.
Not too long after, I got an opportunity to spend a whole day behind the wheel of the GT350R on track where I was really able to focus on what the carbon wheels were doing and exactly how much they added to the overall performance of the Mustang. And the answer was that they actually added a lot.
Or, more accurately, subtracted.
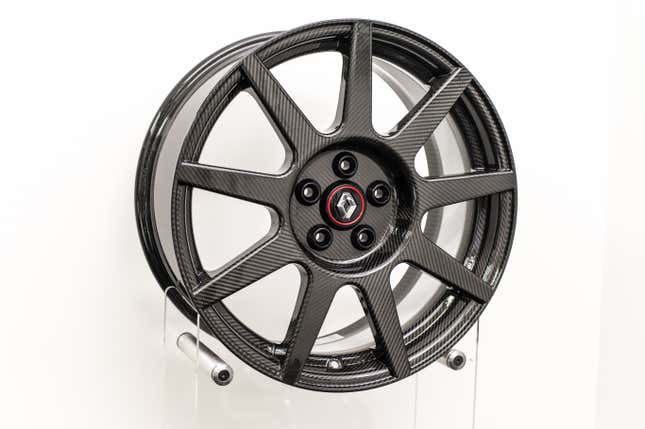
A set of original-equipment forged wheels (19 x 10.5 inches up front and 19 x 11 inches in the rear) for the GT350 weighs in about 33 pounds per wheel. The carbon fiber GT350 wheels (19 x 10.5 inches front, 19 x 11.5 inches rear) are just 18 pounds each by comparison.
According to the principles of math, that’s a savings of 15 pounds per wheel—vital pounds shaved off easily where it counts. Even more impressive, the GT500 wheels (which are the latest generation design) weigh almost the same as the GT350R wheels, but are a full inch bigger in diameter.
They’re just not cheap. On the GT500, the wheels are part of an $18,500 option package, as much as a decent used Honda Accord—or even a Mustang that’s a couple years old. The wheels are standard on the GT350R, though replacements are $3,433 each up front and $4,053 each for the rears, according to Car and Driver.
Worth it? If fighting the laws of physics is your bag, then maybe.
Our buddy Jason Fenske over at Engineering Explained did a very informative video a few weeks back detailing this very subject. But Jason’s main focus was on the overall mass of a car. While the mass of a wheel does, of course, contribute to overall vehicle weight, wheel weight is far more important because a wheel’s mass is additionally rotational and unsprung.

The rotational mass (aka “moment of inertia” or “rotational inertia”) of a wheel is the simply the torque needed to rotate said wheel. The more you can decrease the mass of a wheel, the easier it is to accelerate and also decelerate any time vehicle speed changes. This means less power is needed from the engine to rotate the wheel, in effect “adding horsepower” and also improving fuel economy as the engine is doing less work.
Additionally, reducing wheel weight increases braking performance as well, as there is simply less mass for the brakes to have to act on.
In addition to rotational mass, a wheel’s mass is also an unsprung mass, meaning mass that is not supported by the suspension (i.e. the chassis, engine, transmission, etc.) Reducing unsprung mass allows the suspension to react more quickly to bumps and other changes in the road surface, easing the work the suspension has to do. This has an additional effect of increasing traction as, with less weight to deal with, it is easier for the shocks to keep the tire in contact with the pavement.
So as you can see, wheel weight is probably some of the most crucial weight in a vehicle. And also one of the most impactful in terms of benefits produced by reducing weight.
For years steel and aluminum have been the go-to materials for wheel manufacturers. Steel is durable and cheap, while aluminum is more expensive but lighter. Looking to save even more weight, some wheel manufacturers have long gone as far as to use uber-expensive magnesium.
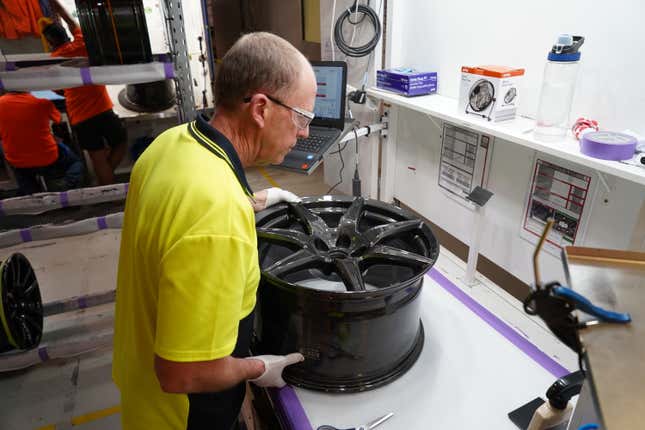
In fact, it’s magnesium that comes closest to carbon when manufacturers are looking to shed pounds. However, the material pricing for such wheels is a huge portion of the cost needed to build them.
On the other hand, carbon fiber reinforced plastic is increasingly becoming (relatively) inexpensive. Traditionally, however, they’re still very labor-intensive to build. This is where companies like Carbon Revolution come in.
Looking for a competitive edge while working on his Formula SAE program at Australia’s Deakin University, Ashley Denmead and his team designed a set of carbon wheels with the help of an outside engineering firm that supported the program. The wheels made a huge performance advantage. Interest piqued, the firm principals would go on to partner with Denmead and co-found Carbon Revolution.
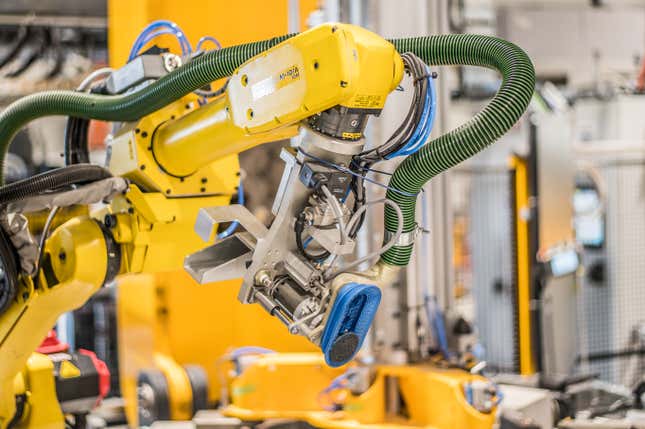
Now just as Henry Ford didn’t invent the automobile, Carbon Revolution didn’t invent the carbon wheel. But like Ford, what it is doing is creating a way to automate the build process, making the wheels better and less expensive by doing so. (Interesting, then, that Ford was the company’s first major OEM customer.) To that end, Carbon Revolution has invested a huge amount of cash to upgrade and expand its facilities located in Geelong, Australia.
The major task to become an OE supplier to a major manufacturer is proving that the part supplied will meet their very demanding engineering specifications (durability, longevity, stiffness, etc.), but you must also prove that you can consistently and reliably produce those parts in volume. And this has been the major stumbling block to getting many new technologies accepted for OE use.
After a lengthy process, Carbon Revolution’s wheels were accepted by Ford for use on the company’s GT350. With demand for the GT350R substantially higher than predicted, Carbon Revolution had its hands full in meeting demand.
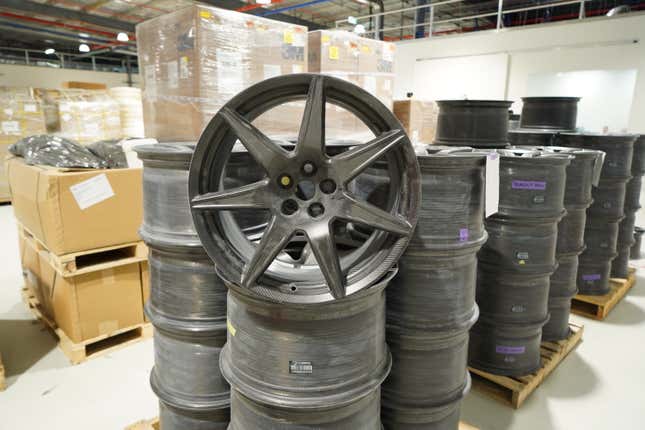
With help from some auto industry veterans, Carbon Revolution was able to win the contract to supply wheels for one of the most demanding automotive companies in the world: Ferrari. The wheel is an option on the 488 Pista and the SF90 Stradale.
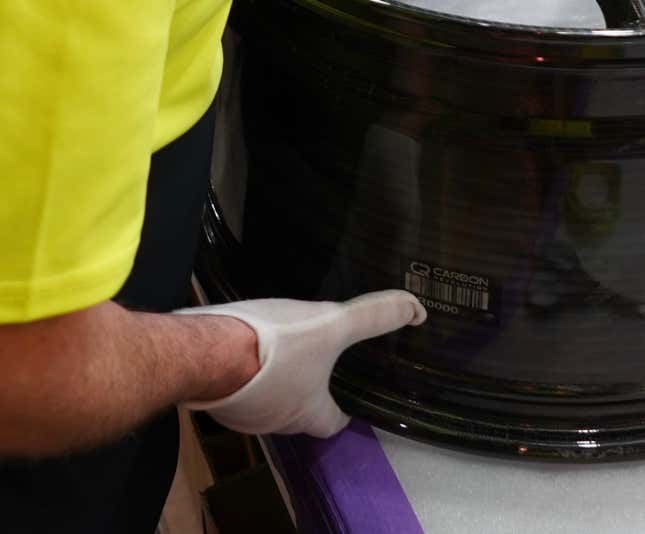
As an example of processes that have improved over time, Carbon Revolution now has the ability to track each wheel produced from the very start of the process all the way through completion. From the beginning of the manufacturing process, each wheel is given its own embedded bar code which enables both Carbon Revolution as well as the manufacturer to track any issues that may arise with the wheel.
But co-founder and Chief Technology Officer Brett Gass told me there are still lots of ill-informed opinions and misconceptions to deal with. Gass said he’s seen and heard concerns about the wheels’ inability to handle impacts like potholes, or what happens to a wheel when it fails.
“Carbon fiber is an inherently strong material,” he said. “It is why (in) many applications, when weight is critical, companies have migrated away from metals to carbon. Formula One monocoque chasses are a great example where the industry moved to carbon fiber to improve safety, increase stiffness and reduce weight. Because of its high strength, carbon fiber composite parts can carry very high loads without permanent deformation. In contrast, aluminum has relatively low structural properties compared to carbon, so an aluminum wheel needs to be heavier to be equivalent strength and stiffness of a carbon fiber wheel.”
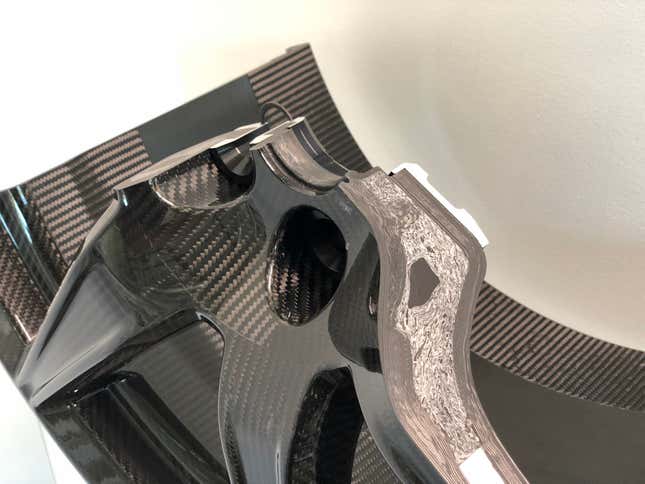
Gass added: “With respect to impact, our wheels run all the same vehicle tests as the metal ones and because of the superior material properties, we can meet the requirements and significantly reduced weights. In a catastrophic event, carbon is very robust. People think that all carbon shatters in an impact. I think this comes from watching F1 wings come off a car at any contact. This is a function of the design of the part, not the material. In a vehicle crash, the carbon monocoque chassis protects the driver as it is designed to do. As you can see in the cross-sections of our wheels, they are very robust sections and designed to absorb a lot of energy.”
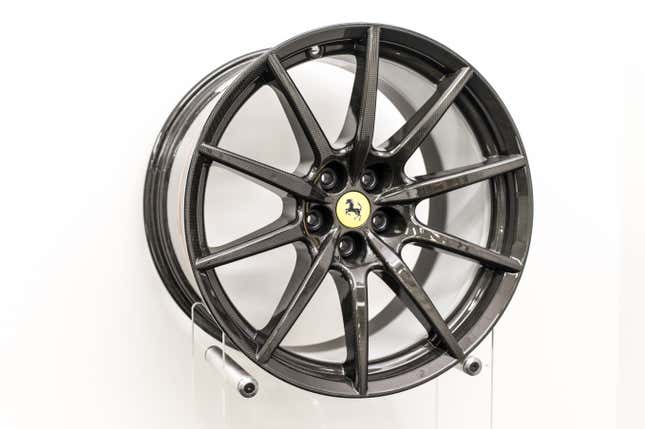
As you might guess, carbon wheels on high-end performance cars isn’t exactly a volume play. But the people at the company tell me they’re thinking beyond supplying niche cars. All of the advantages of a carbon wheel can theoretically speak to a different (and much larger) audience.
With their inherent weight being a critical issue, the coming surge of electric vehicles would stand to benefit substantially from the weight savings that a carbon wheel offers. Not only could that help reduce overall weight, but it could increase vehicle efficiency—in this case battery range—by reducing rotating mass.
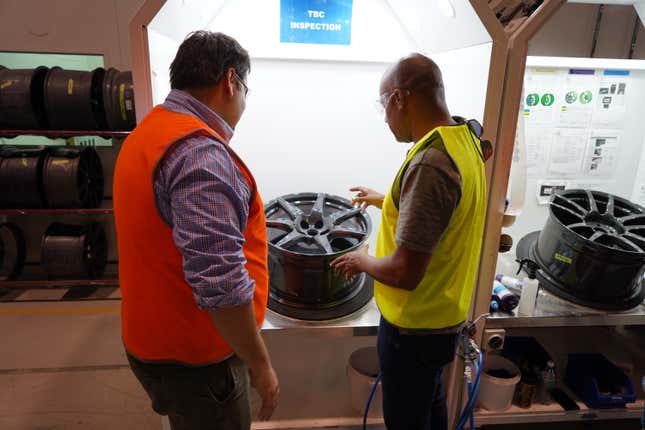
So the next steps are to gear up production to supply EV manufacturers in volume. With any luck, the company hopes carbon fiber wheels won’t look out of place on a Nissan Leaf in a few years’ time.
So keep buying those GT500s. You’ve got to do your part to help the environment.