Manufacturers are investing huge sums into battery technology to maximize the range and performance of new electric cars. However, if you pop the hood of a modern EV, you might find a regular old 12-volt car battery. That may be a confusing experience, but fear not — we’ll explore why that’s there, and uncover the secrets of an electric car’s 12 volt systems while we’re at it.
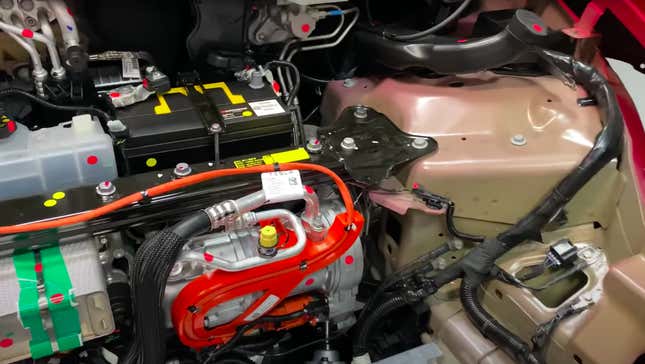
Most electric cars get around with just one big, high voltage battery pack full of rechargeable lithium cells that drive the motor. But, EVs also have a regular old 12 volt lead-acid battery, just like the one in your fossil-fueled car. This may seem odd or redundant, but the old-school battery serves multiple important purposes. One of the problems with a big, high voltage battery is that it can be quite dangerous. Isolating the battery from the rest of the car’s electronics is important. To achieve this, electric cars use a contactor.
The Contactor: It’s All About Safety
The contactor allows the main battery power to the vehicle to be shut off when the car is in an accident, being worked on, or simply not being driven. It’s an important safety measure that helps prevent electrical fires and/or electric shocks, and allows the main traction electronics to be de-energized when not in use. Contactor is a fancy word for what is essentially a big switch that controls the flow of current from the battery pack. A contactor is turned on by supplying voltage to a coil. This coil acts as an electromagnet, moving a larger set of contacts, which allows current to flow out of the high-voltage battery. Switch the coil back off, and the contacts spring apart, breaking the circuit and disconnecting the battery. It’s just like a big relay, basically.
The need for such a device poses a problem: How do you energize this contactor in order to connect the main traction battery to the rest of the car’s electronics? An easy way to do this is to use a nice, reliable 12 volt battery. Fancier solutions would work too — such as modern Li-Ion 12V batteries — those are already shipping in some cars. But with lead-acid car batteries already proven and rated to last in an automotive environment, and available all over the world, why reinvent the wheel? Or the battery, for that matter.
The other main area where the 12-volt battery helps is in all the ancillary systems in a modern car. Things like blower fans, electric windows, headlights, and infotainment systems have all historically run on 12 volts. They all work great as-is. Engineering an electric drivetrain is strenuous enough, so it makes sense from a cost and durability standpoint to use existing, proven designs for systems that can largely carry over.
Electric cars use huge voltages for their main traction batteries - anywhere from 300 to over 800 volts. Higher voltages allow for lower currents for a given power level, and lower currents cut down on resistive losses for the main power circuits. But high voltages are undesirable for other uses, as they require more care in terms of insulation and protecting cables from damage. These high voltages are dangerous to people and other equipment, so any such cabling must be produced to a high standard and insulated properly to avoid issues.
It’s also difficult to switch high voltages; particularly with direct current from batteries, switches tend to arc when flipped and get damaged, and semiconductors to handle higher voltages inherently cost more. There are vague plans to switch more cars over to 24 V or 48 V systems in the future, but these voltages are still much lower and safer than modern high voltage batteries for regular use. For now, though, 12 volt accessories are the norm.
For more information on the presence of 12 volt batteries in EVs, we reached out to an engineer at a major OEM. He broke it down, saying:
If we take the EV bit out for a second 12V systems are used in vehicles to supply power to various modules and accessories we find in cars. 12V systems were not always the answer, if we look back 6V used to be the answer, many military applications use 24V and 48V is starting to creep in, but at this point 12v is most prolific. Regardless of the voltage we need some sort of power supply to run our modules, and there are A LOT of 12v parts sitting around, and the automotive industry loves to re-use parts.
Yes, you could have a radio that is supplied by 350V but that’s expensive and as I mentioned before there’s a lot of 12v designs ready to just plop in.
There’s No Alternator In Aa EV, There’s A DC-DC Converter
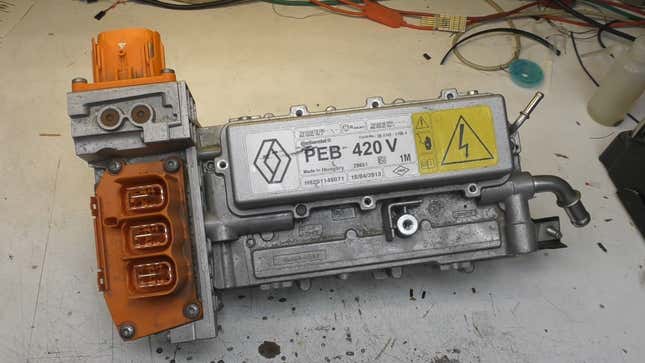
Thus, having a source of 12 volt power for all these accessories is a must. However, as anyone who’s ever had a busted alternator knows, you won’t keep things running for long on just a regular car battery. EVs need a way to keep their 12 volt battery charged, and to help supply power to all the accessories when they’re running. EV batteries output direct current (DC), so simple AC transformers are not an option to step the voltages down from the main battery to charge the 12-volt one. Instead, the job falls to the DC/DC converter.
You might ask: Can’t we just use a DC/DC converter to run everything and forget the 12V car battery altogether? Well, no. You still need the 12V battery to turn on the contactor that connects the high-voltage traction battery to the rest of the car. On top of that, regulations get sticky, too. Our engineering contact notes:
Now you could only have a DC-DC converter that is always on to power the various modules but being always on that would mean the HV battery would be slowly discharging over time, always. This isn’t really ideal from a storage scenario and then there are some regulations (ECE-R-100 and FMVSS-305) which state in the event of a crash the HV bus must be discharged in a certain amount of time and the HV battery disconnected from the rest of the vehicle. So again we have some situations where we want systems to be powered while the vehicle is “off” and this is where that 12v battery comes in.
I’ve been an electronics fanatic since I was just a few feet high. Teaching myself to understand the basic concepts has served me well, as modern cars are as reliant on electronics as they are on mechanical principles. It’s also made me popular with anyone that needed help installing a car stereo. Let me lay down the basics of how DC-DC converters work so you might better understand what’s going on under the hood of your garden-variety EV.
How DC-DC Converters Work: It’s All About The Switching
There are a wide variety of DC/DC converter designs, some capable of turning a small voltage into a bigger one (boost converters), turning a big voltage into a smaller one (buck converters), or doing both (amazingly, called buck-boost converters). For electric vehicles, a buck converter is the part for the job, stepping hundreds of volts from the main battery back down to the nominal 12-14ish volts desired to charge the 12V battery and run accessories.
Some manufacturers do use bidirectional buck-boosts in this application for niche edge cases. However, when stepping down the high traction battery voltage to the 12 volts for the accessory subsystem, the mode of operation is by and large identical to a regular buck converter.
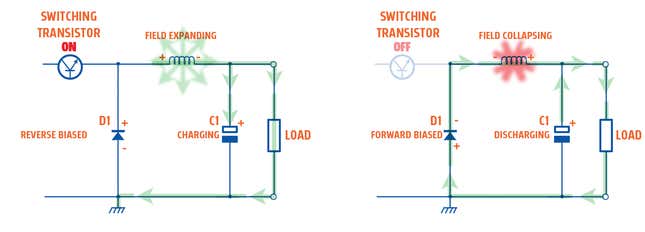
A buck converter takes a DC supply at the input, and puts out a lower DC voltage to the output load. In our case, the DC supply is the main battery voltage, sitting at many hundreds of volts. Our output load is our 12 volt accessory system. The buck converter steps the voltage down using a diode, an inductor, a capacitor, and a transistor that’s switched by some additional circuitry. For those unfamiliar, a transistor is a special type of electronic switch that can be turned on to allow current to pass or turned off to stop the flow. In that way, it’s similar to a contactor, but is electronic instead of electromechanical, switches much faster, and works at much lower voltages and currents.
The diode is a part that only lets electricity flow one way. The inductor and capacitor are devices that store electrical energy in magnetic fields and electric fields, respectively. For reasons that are best explained with complex physics going well beyond the scope of this article, inductors tend to oppose changes in current, while capacitors oppose changes in voltage.
So how does the buck converter operate? When the transistor is first turned on, current begins to flow from the higher voltage DC supply (in our case, the battery). The positive voltage is present at the cathode of the diode, which prevents it from conducting, and it has no effect on the circuit at this point. Current from the battery also flows into the inductor. The inductor begins storing some of this energy, and power begins to flow through the inductor to the load, as well as to the capacitor. As the inductor resists instantaneous changes in current flow, the capacitor begins to charge up gradually rather than all at once, increasing in voltage over time. As the capacitor is in parallel with the output, the output voltage slowly increases.
After a set time, the transistor is turned off, breaking the connection to the high voltage DC supply. The side of the inductor that was receiving positive charge from the battery is now seeing nothing. The inductor wants to keep the current flowing, however. Thus, it switches from storing energy from the battery to supplying energy itself. Thus, it develops a negative charge at its input side, and a positive charge at the output terminal to keep the power flowing in the same direction. The negative charge at the input side is also connected to the diode, now allowing it to conduct. With the circuit completed, the energy previously stored in the inductor’s magnetic field keeps the current flowing, stopping the voltage from simply diving straight to zero.
Then, after a period, the transistor is switched back on, and the inductor and capacitor charge up again. The timing of the switching—also known as the duty cycle—is key to how much the output voltage is stepped down. This is the ratio of how long the transistor is on versus how long it is switched off. If the transistor were on 100% of the time, the output voltage would rise to the input voltage once the capacitor was fully charged, and stay there. If the transistor is off all the time, the output voltage would be zero. The output voltage is, in a perfect buck converter, directly proportional to duty cycle. Thus, the desired duty cycle equals the desired output voltage divided by the input voltage. This means that to step down 400V from a traction battery to 12V - we get a duty cycle of 0.03. This means that we turn the transistor on 3 percent of the time, and keep it off 97 percent of the time.
When a buck converter is operating on such a large step down, the off period is very long - as we’ve seen in our example. In these conditions, the inductor can run out of magnetic energy to keep the circuit flowing. When this happens, the capacitor begins to drain itself of energy too, maintaining current flow until the transistor comes back on again. This is called discontinuous operation, though buck converters are also perfectly happy operating at more even duty cycles without issue.
The basic theory behind the buck converter takes some wrapping your head around, but the reality of how they work is even more complicated. There are electromagnetic noise issues to contend with, thermal issues, and it’s important to focus on efficiency too. Engineers optimize all parts of the operation with techniques such as switching the transistor on and off at high speeds - often in the tens or hundreds of kilohertz. This also has the benefit of reducing ripples in the voltage output as the capacitor and inductor charge up and down.
Diodes can also be replaced with transistors switched by external circuitry to mimic a diode’s one-way-valve operation. This is due to the relatively high voltage drop of diodes in the real world - usually 0.3-0.6 volts - which can waste huge amounts of power in a high current application. Transistors can offer voltage drops well below 0.05 volts, saving energy and running cooler, too.
There are numerous, complicated ways to improve a buck converter and numerous ways of configuring them to run in reverse, too but that’s all beyond the scope of this post. But the basic concept at play remains the same - switching on and off a voltage to an energy storage device at a certain duty cycle lowers the voltage at the output.
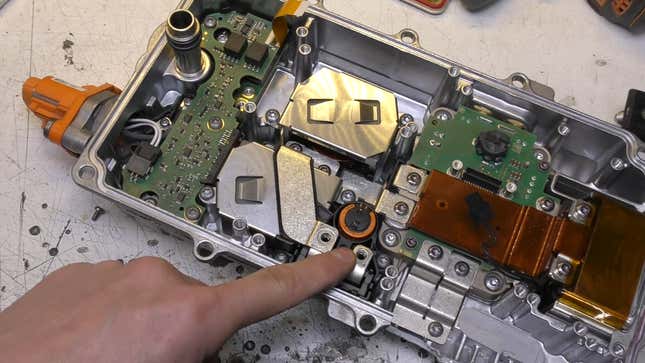
Mike of the YouTube channel mikeselectricstuff tore down a relatively low-powered unit from a Renault Zoe last year, revealing it to be a densely packed and inordinately complicated device. He points out the obvious features - the large capacitors and inductors made of fat copper bars bent into coils. The video also goes to show the safety measures built into the hardware, like the special high-voltage connectors with extra pins to check that they’re properly hooked up.
These are not cheap components, either. The average alternator in a modern ICE car can output in the realm of 150 amps. Talking about accessories only, electric cars have similar electrical demands to their ICE forebears in this area, so the DC/DC converter must be able to deliver a similar amount of current. This means plenty of fat conductors are required to carry the current, and high power transistors are key. These are often hefty IGBT or MOSFET parts, with bare silicon dies assembled directly onto special thermally conductive boards.
This helps reduce thermal insulation effects from plastic packages on individual components and reduces losses through long component wire leads, too. The DC/DC converter is often built into a single module with the charging hardware, as both need to connect directly to the high voltage battery and both benefit from water cooling their hot electronics.
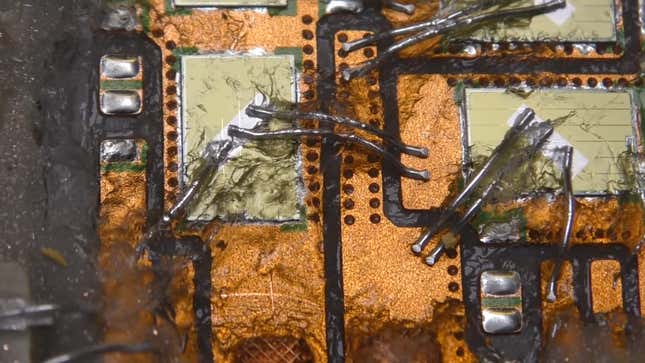
Thus, the humble 12 volt lead-acid battery remains a key part of almost all modern electric cars, working in concert with a high-power DC/DC converter and 12 volt accessories to provide you with all the usual amenities you expect in a modern car. Technology will continue to march onward, and we may see standards change to higher voltages or new battery types. However, we’ll be relying on low-voltage accessory subsystems for the foreseeable future, and now you know how they work!