The Cadillac ATS-V's Cooling System Is A Masterpiece Of Engineering
The Cadillac ATS-V's cooling system is hard to ignore. Just look at this photo. You’ve got heat exchangers all over the place.
Cadillac gave me an ATS-V for a few days, and I drove the crap out of it. But I also studied it, and was left awe-struck by the cooling system. There are six heat exchangers mounted to the front of the car— three in the center, two outboard, and one even lies flat, flush with the bottom of the car. Here's how it all works.
Modern cars' engine bays are crowded and blocked off by big plastic covers, making looking at awesome mechanical bits really difficult. The good thing, though, is that the coolest system in cars is always exposed for the eye to see, because if it weren't, it wouldn't work at all.
I'm talking about the cooling system, and on the Cadillac ATS-V, it's hard to ignore. Just look at the shot above. You've got heat exchangers all over the place.
Out front, there are six in total on this manual 3.6-liter twin-turbo ATS-V: three comprise the cooling module, which is mounted traditionally, right in the center; two are remote mounted, hidden behind the two outboard openings in the lower fascia; and one is sitting flat, nearly level with the bottom of the car, just in front of the cooling module.
Cooling Module
Right in the center in front of an electric fan (probably an 850 Watt fan), sit three heat exchangers. The rear-most one (labeled 3 in the picture below) is the standard air-to-coolant heat exchanger that keeps the engine from overheating (the radiator). Next comes the condenser, which is used to cool refrigerant in your air conditioning system. These are fairly normal to see in an ordinary cooling system.
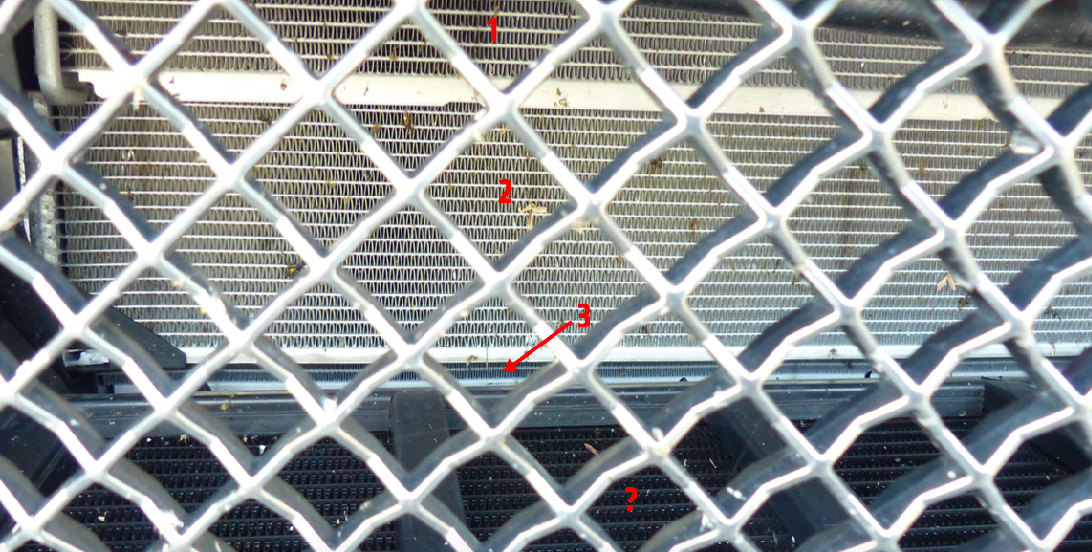
In front of the condenser is something that you don't see that often even in modern cars: it's a low temperature radiator, or LTR, and its job is to help lower the temperature of the intake air after it goes through the turbos.
Remote-Mounted Low Temperature Radiators
That low temperature radiator out front gets some help in cooling the air charge via two remote-mounted low temperature radiators mounted outboard on the lower fascia.
All three low temperature radiators—the big one in the center and the two small ones outboard— are plumbed together with a 35 Watt coolant pump circulating fluid through them and then through two heat exchangers in the intake manifolds.
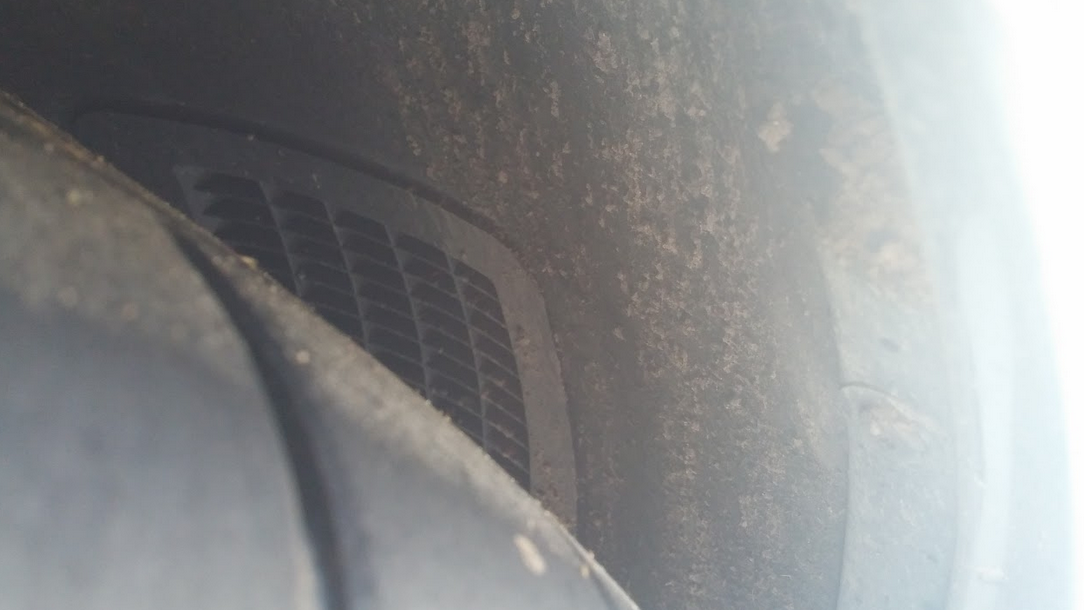
As intake air is compressed by the turbo's compressor, it heats up. To cool that air to ensure stable combustion and maximize volumetric efficiency, many traditional turbocharged cars send the hot air to an air-to-air intercooler (or "charge air cooler") out front.
Instead of doing this, some automakers—like Cadillac— are going to air-to-coolant intercoolers built into the intake manifolds, and these heat exchangers are fed cold coolant from low temperature radiators via electric pumps. I asked an old engineering friend and thermal systems engineer Mitch Zajac why automakers are moving away from traditional air-to-air intercoolers (ACAC) and towards liquid-to-air intercoolers (LCAC) with LTRs, and he said:
An ACAC system can have more than twice the air volume as compared to a LCAC system – increasing turbo lag. The overall cooling capacity of the ambient air side heat exchanger is also lower in an ACAC system – comparing air to air vs air to water heat transfer.
He went on to suggest that LCAC systems can also help with launch performance, since coolant has more "thermal inertia," so it has potential to remove heat from the hot post turbo-compressor air charge even if there's little airflow across the LTR (because the car isn't moving). He went on, saying:
LTR/LCAC systems take up less under-hood volume, reduce front end overhang, and present potential opportunities for the addition of other liquid cooled components.
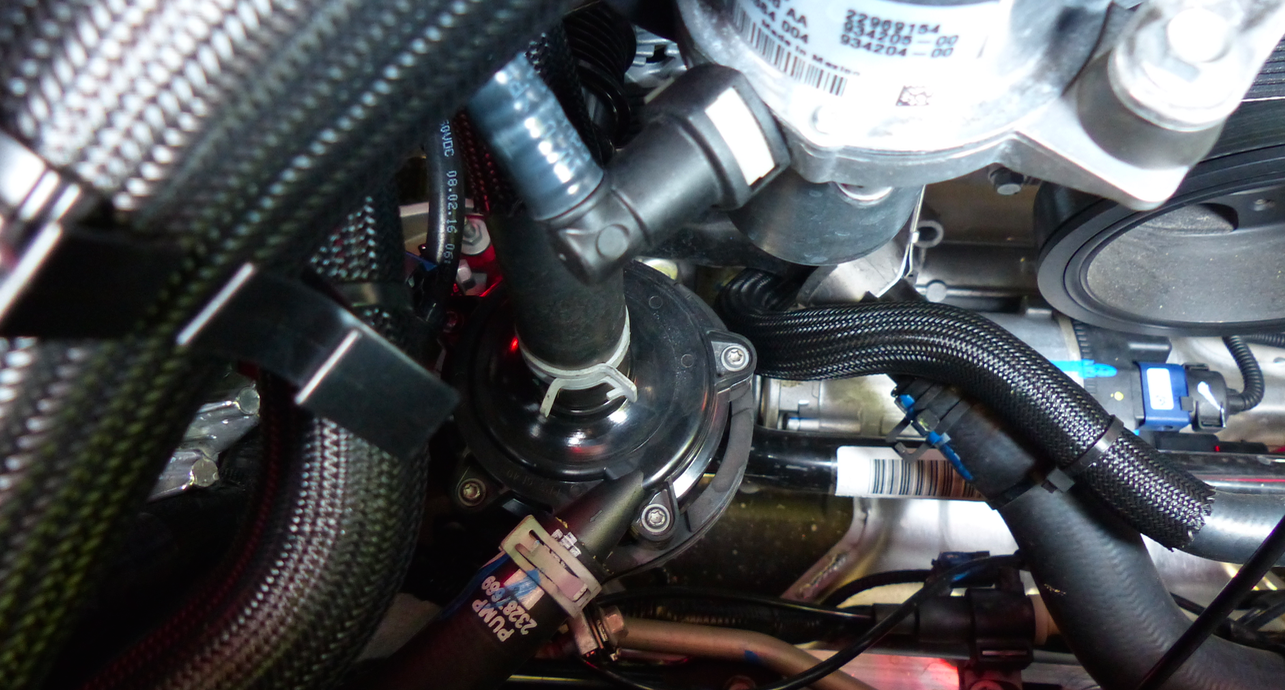
On the Cadillac, cold coolant from the three aforementioned low temperature radiators is pumped via the 35 Watt pump shown above and into the heat exchangers in the intake manifold. The hot post-turbo compressor air then transfers its heat to the coolant, and the cooler air enters the combustion chamber. The now-hot coolant from the intercooler flows into the three low temperature radiators out front, so it can cool and head back into the intake manifold to continue cooling the intake charge.
Bottom-Mounted Transmission and Rear Diff Cooler
The most fascinating part of the ATS-V's cooling system is the bottom-mounted trans and diff cooler. I've never seen anything exactly like it. This thing is literally mounted flush with the belly pan, just inches from the ground.
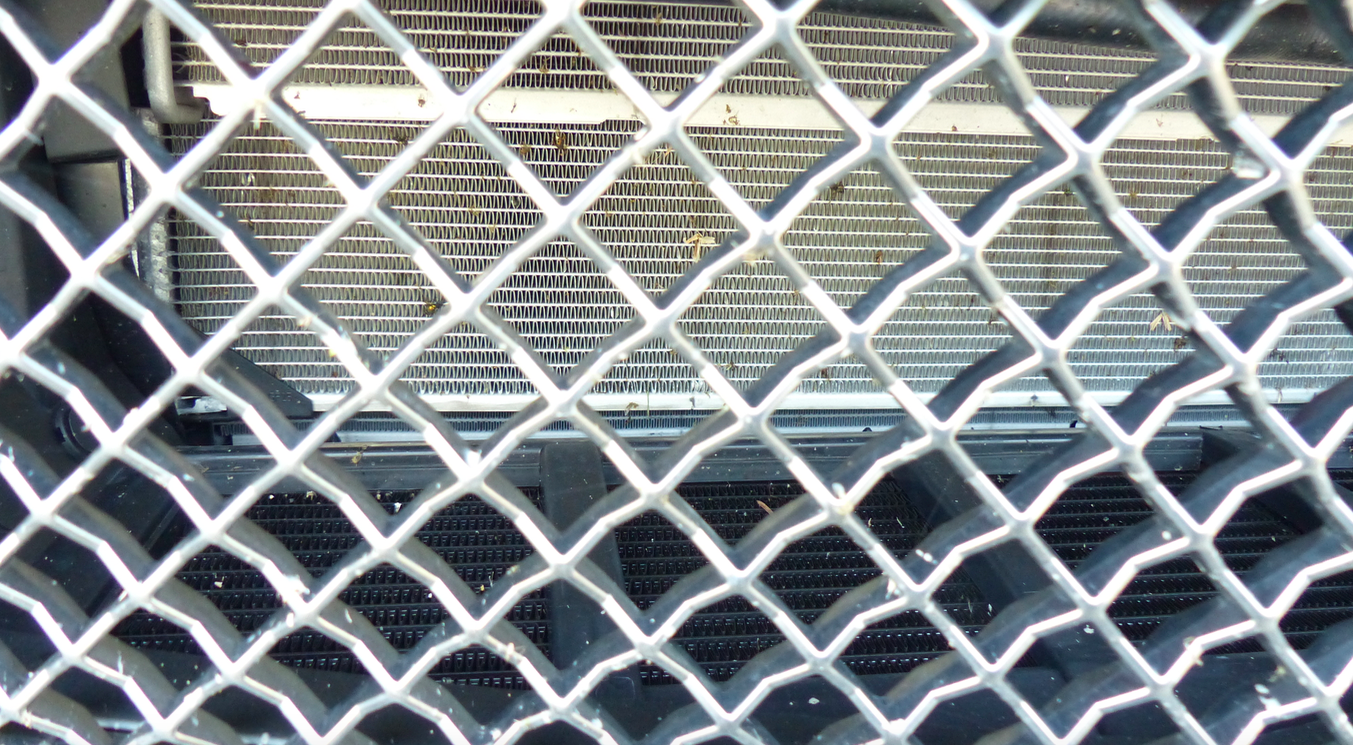
The way this works is clever: air enters through the grille and is channeled via side, top and bottom "seals" into the cooling module (radiator, condenser, LTR). The problem is, that air really doesn't want to travel into the cooling module, as that's a rather restrictive path with all those fins and tubes in the way (not to mention the underhood, which tends to build up a positive pressure).
That's why having good seals around a cooling module is crucial for airflow: the air will go to the path of least resistance (the lowest pressure). In this case, Cadillac is taking advantage of that fact, and has cut holes in the bottom seal of the cooling module.

As you drive the car, oncoming air slams into your cooling module's heat exchangers and creates a positive pressure, while airflow going under your car is at a lower pressure. DeltaP drives airflow, so air goes through the slots in the seals, and right through that flat-mounted heat exchanger.
This method isn't perfect, as Cadillac's chief engineer Tony Roma told me via email that it does add front end lift. Still, he said that's not a concern on this car, as the engineering team "developed the whole cooling and aero package as a system."
Once that air is channeled through that heat exchanger, it cools gear oil, which is sent into the differential and then into the transmission.
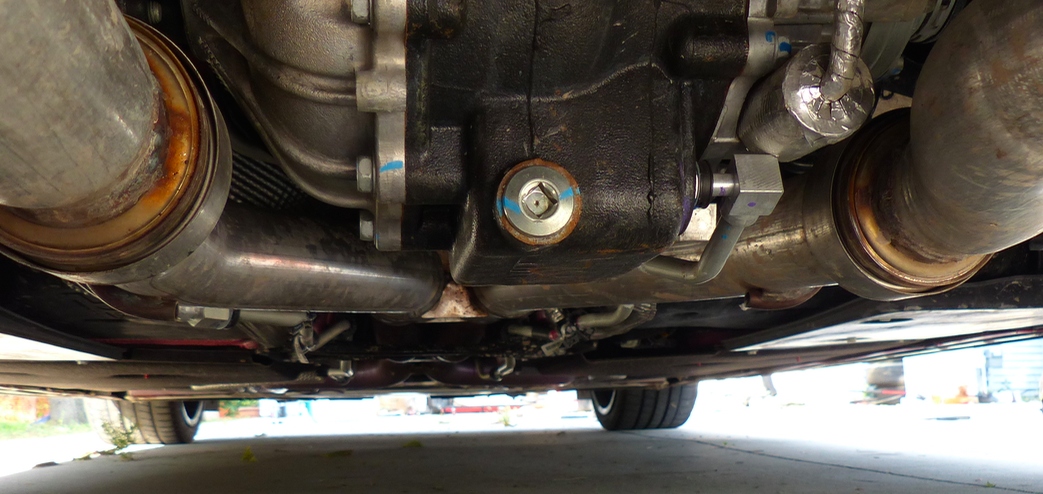
Yes, that's right. The oil lines go all the way from the very front of the car to the rear— a bit of a weight and complexity hassle. But Cadillac's chief engineer said it had to be this way, as there simply wasn't enough airflow under or in the rear of the car. Here's another look at the routing:
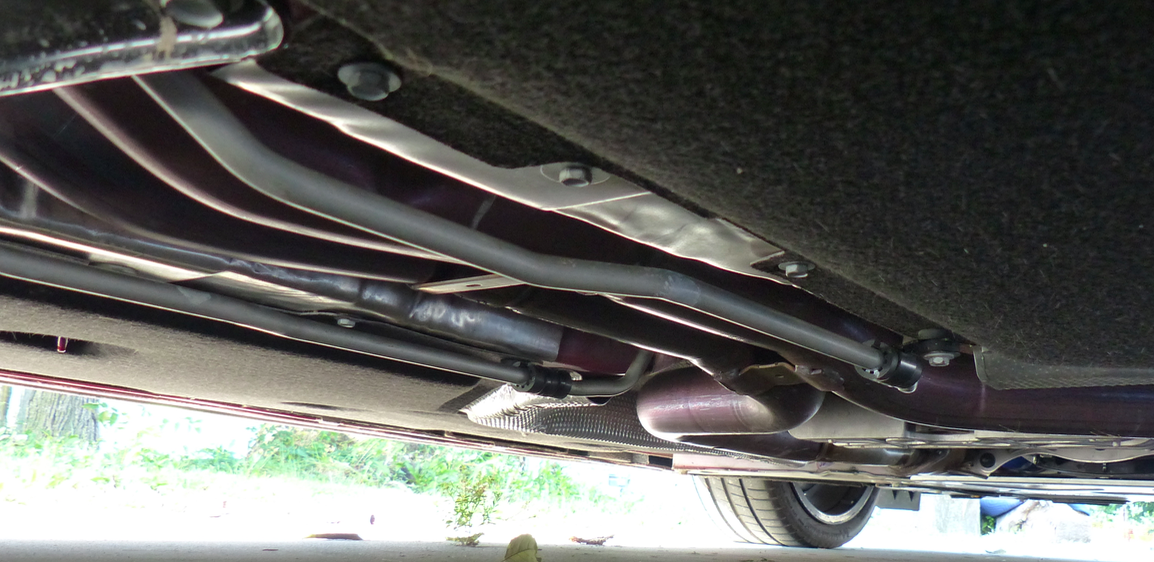
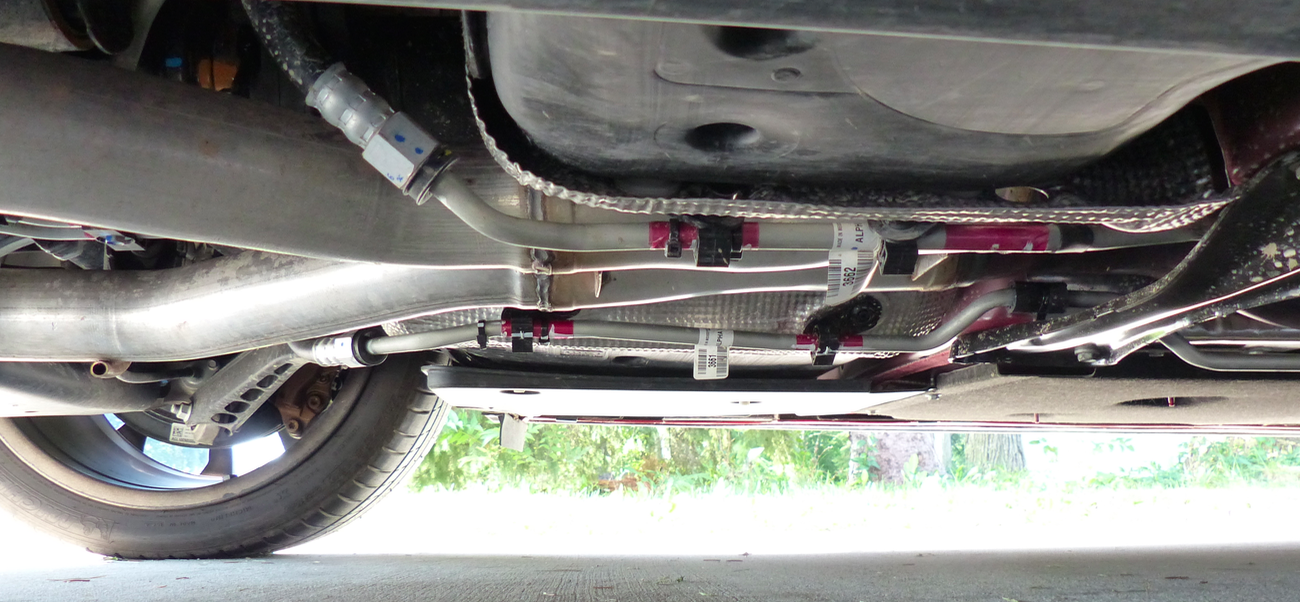
Hood Heat Extractor
The big ol' hole in the hood is there for a couple of reasons. It's meant to lower the underhood pressure to facilitate more airflow through the heat exchangers. Remember that bit about how oncoming air doesn't want to be forced through dense heat exchangers and into a crowded engine bay? Well, this extractor helps alleviate that problem.
It's simply easier to send air through the cooling module and into the engine bay when there's a hole in the hood for the air to vent through. Otherwise, the underhood pressure buildup will deter airflow.
The ATS-V's chief engineer also says the hood vent works to reduce front lift and counteract the effect of that trans cooler opening in the bottom seal.
Brake Ducts
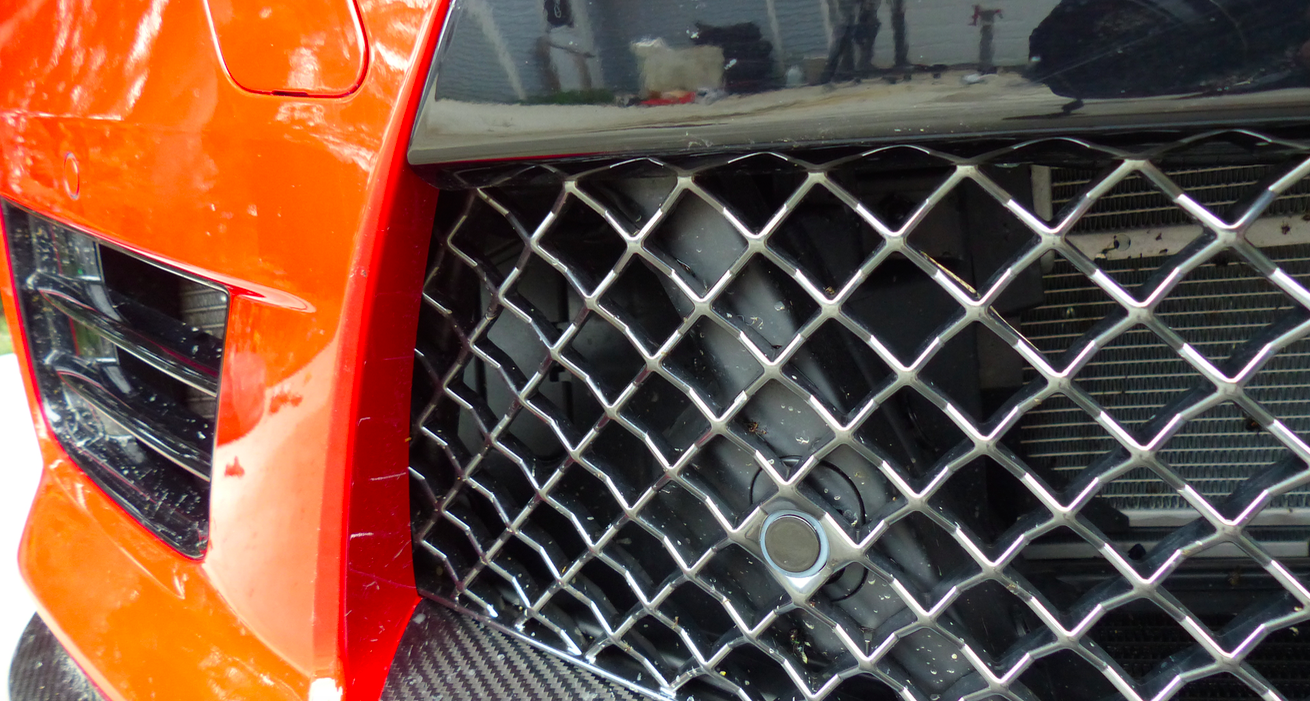
It's hard to see here, but on the outboard sides of the the center lower grille opening are these two "scoops" that channel air through a brake duct, which travels back through the wheel house and keeps the rotors and pads from overheating and the fluid from boiling.
If the pics or my descriptions aren't enough to convince you how baller the ATS-V's cooling system is, here's Dave Leone discussing a couple of the things I mentioned:
I know, cooling systems aren't sexy. They're just oil, coolant, heat exchangers, pumps, fans and ducts.
But if there's any cooling system even close to deserving that adjective, it's definitely the ATS-V's.
Correction: This article originally listed Cadillac's chief engineer as being Dave Leone; it is actually Tony Roma. The story has been updated.