Porsche's 3D-Printed EV Parts Look So Damn Cool
Porsche has been making more and more parts using 3D printing, including a new electric drive unit the company showed off earlier this month. Honestly, it looks sick.
Porsche's latest 3D printing project is a fully integrated electric drive housing that contains both an electric motor and a two-speed gearbox. The drivetrain unit is made of an aluminum alloy and is reportedly strong enough for use in Porsche's super sports cars. And even its production process looks cool.
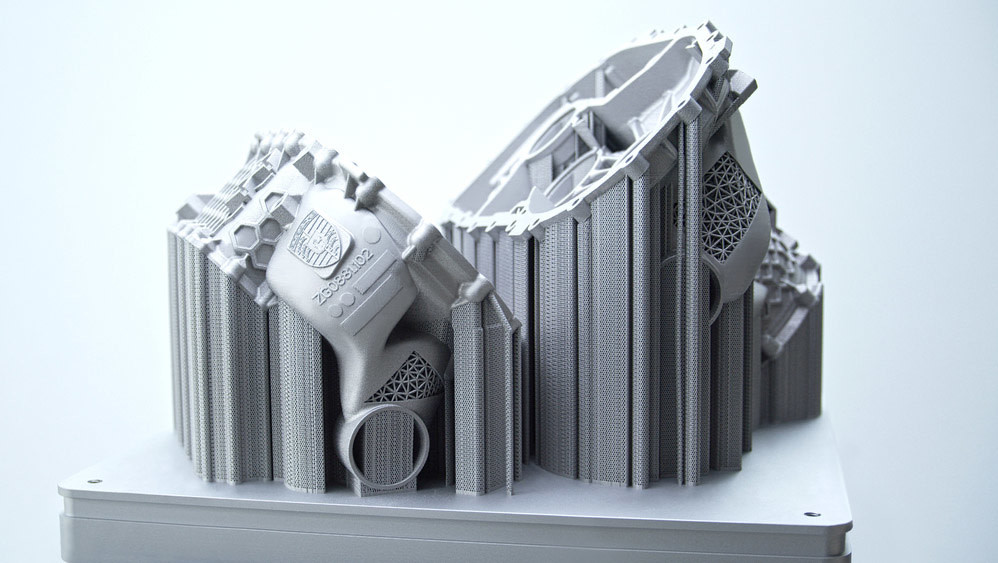
The carmaker used what it calls a laser metal fusion process (LMF), in which a laser beam heats and melts the powder surface corresponding to a part contour and then proceeds layer by layer with an aluminum alloy powder. The process enabled Porsche's engineers to optimize for heat transmission and test for loads in real-time.
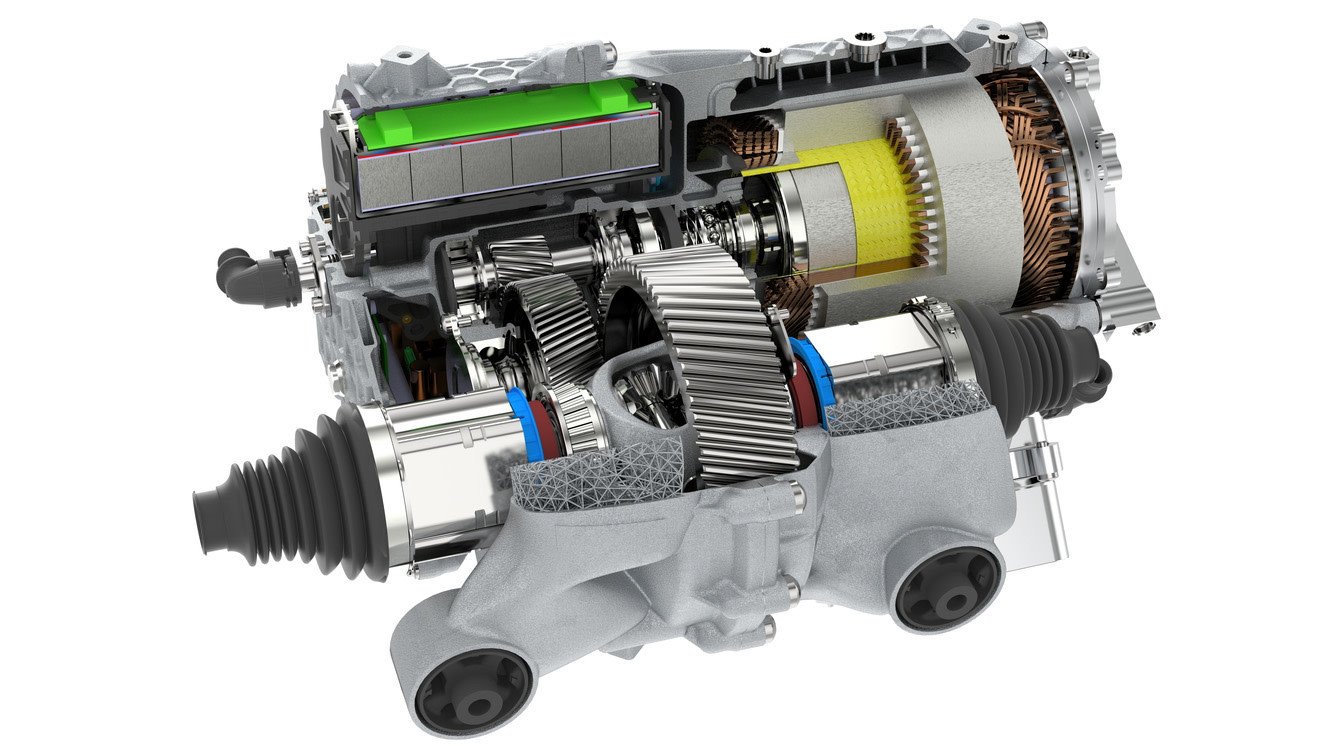
The final printed housing is 10 percent lighter than a traditionally cast part. Its lattice structures increase the stiffness, and despite it being only 1.5 millimeters thick it's stronger than a similar part would be without the honeycombs.
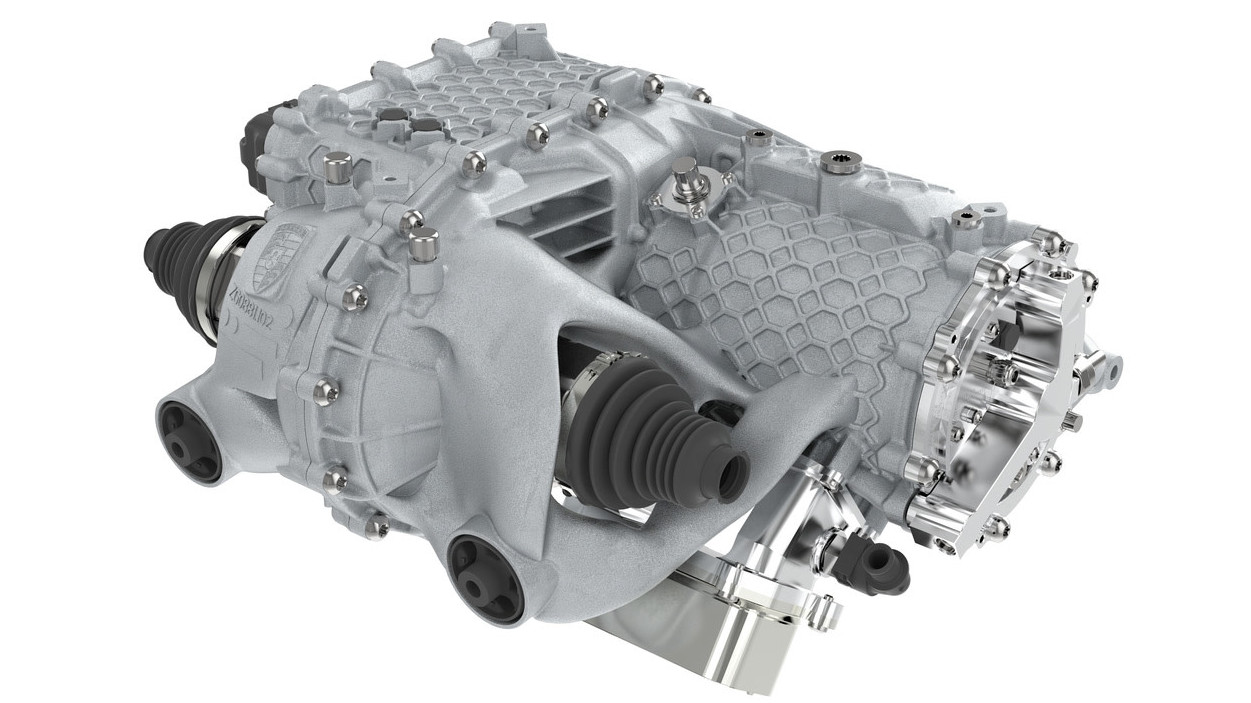
This is a natural next step for the carmaker, which 3D-printed pistons and put them through the most grueling test in the 911 GT2 RS. Like the drivetrain housing, those pistons were printed using LMF, and the process yielded both a lighter end-product and a better optimized one. The pistons had a cooling duct that would have been impossible to integrate through conventional production methods.
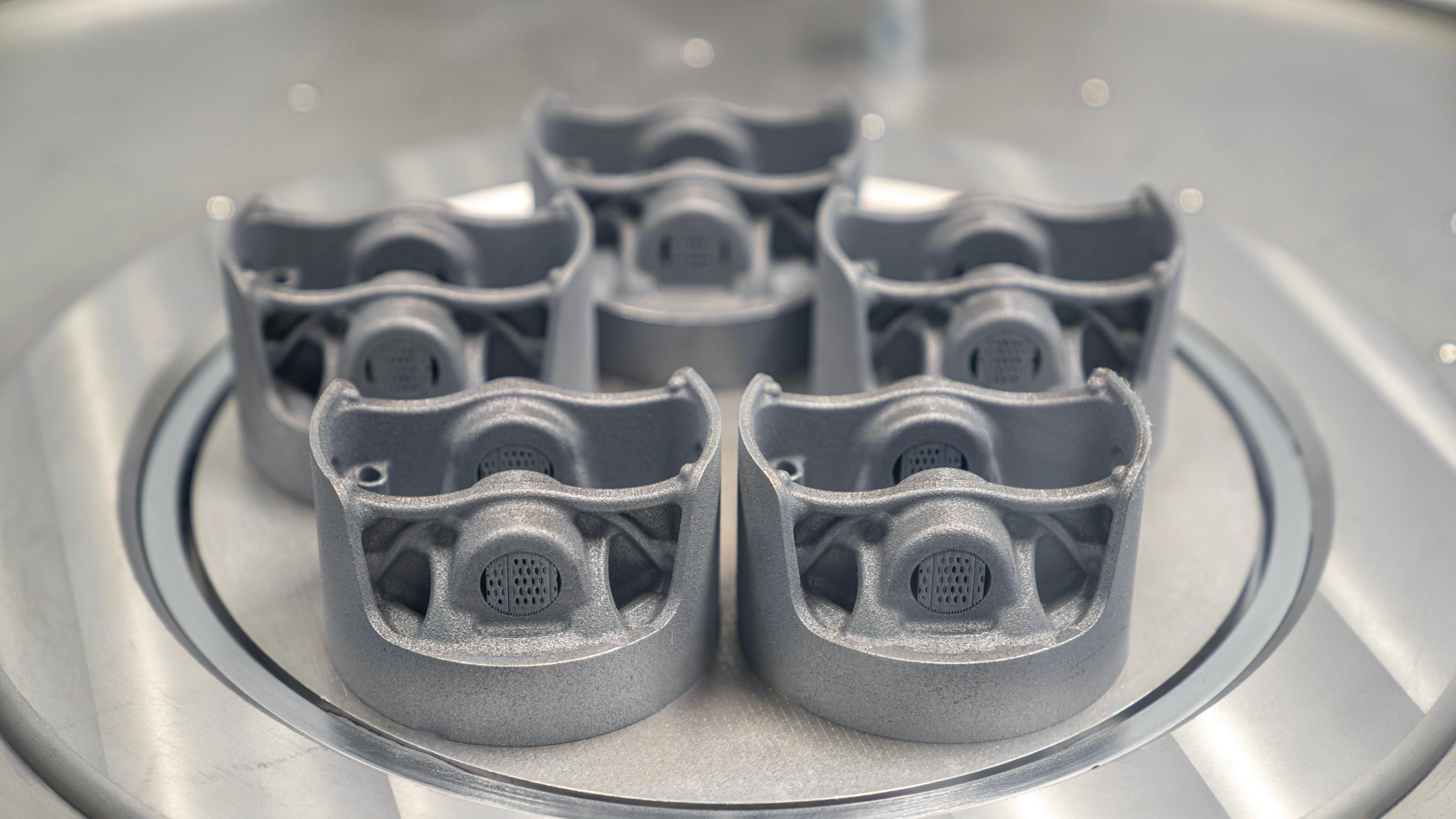
Porsche mentioned the possibility of 3D printing for custom applications and spare parts. It's amusing that carmakers throw in this little tidbit, usually at the end of these announcements with a brief reference. It's kind of a gimme for enthusiasts who dream of retrofitting older vehicles with new parts. In the case of this integrated drivetrain, however, it wouldn't be a matter of just dropping a couple into a classic 911 and calling it a day.
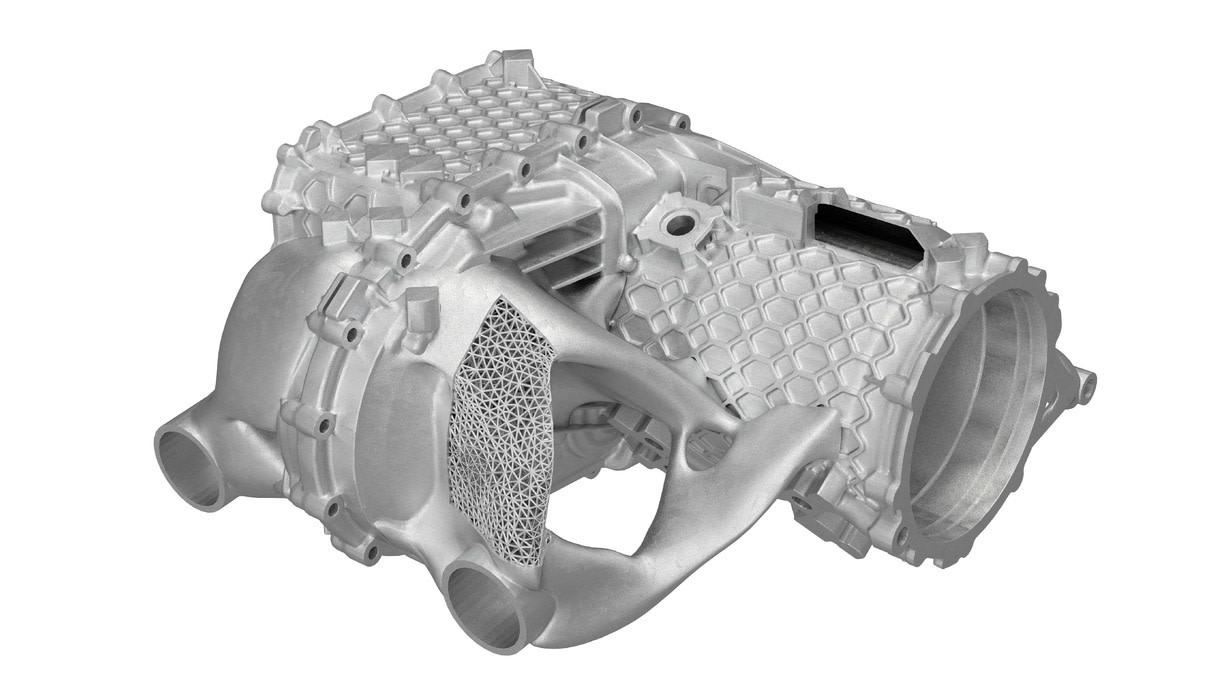
Porsche specifies that the electric drive is designed "for use on the front axle of a sports car." It seems likely that the prototype, or another like it, is intended as R&D for its upcoming EVs, rather than in its internal-combustion models.
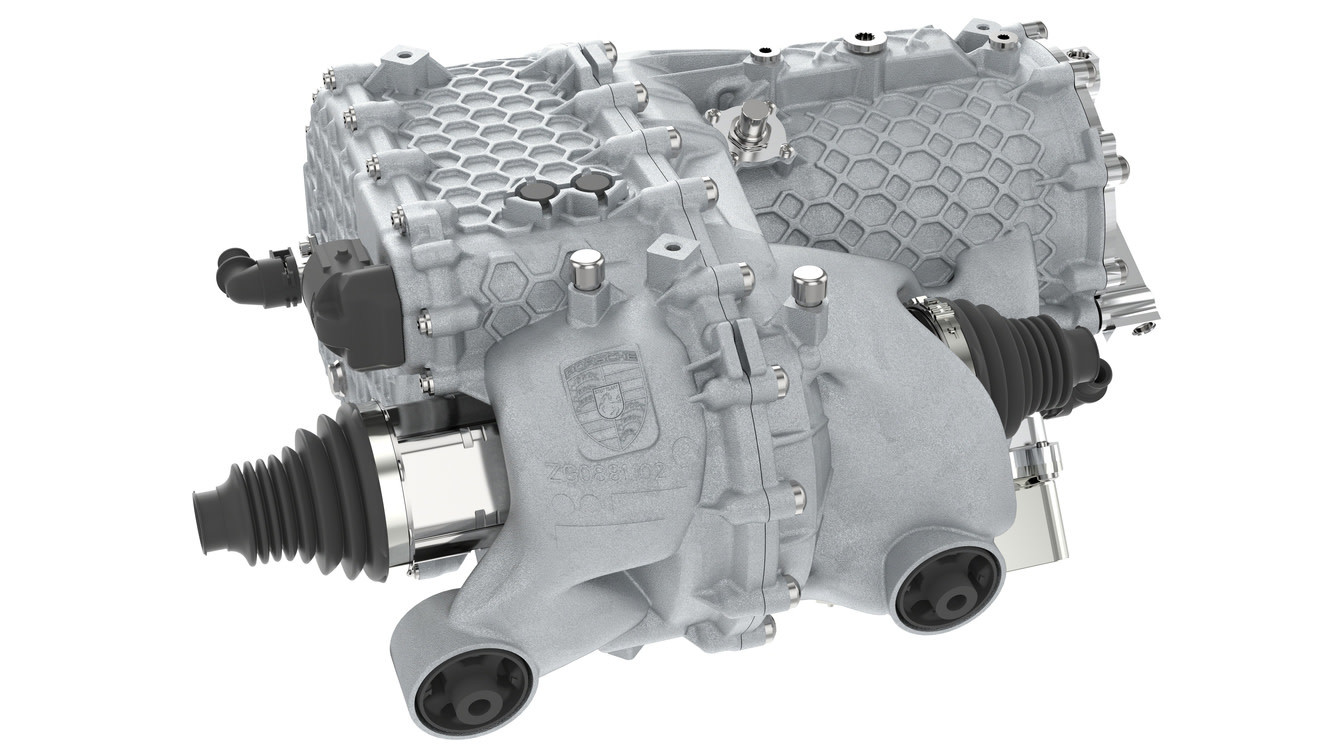
Notably, these processes are still more or less seen as bolstering traditional machining production. They are currently not the primary form or mode of production, but I wonder when they will no longer be seen as adjacent steps and make the transition to production at scale. A recent trend among carmakers is their shift from calling it simply 3D printing to "additive manufacturing," in reference to the layered nature of the production.
The carmaker is already open to the possibilities that 3D printing introduces, and the process has followed an impressive trajectory at Porsche. So far, Porsche has 3D-printed classic spare parts, bucket-seat sections, pistons, and now an entire electric drive housing.
We've gone from 3D printing seeming like a novelty, or something with limited applications, to producing parts for flagship sports cars. The process is quickly maturing as a form of production and carmakers are noticing the benefits it provides, namely "agile [...] and flexible production."
Unlike GM, however, Porsche is not announcing a dedicated facility or the addition of thousands of square feet of 3D printing space. But just the notion of the Stuttgart company experimenting with these highly integrated designs is exciting for the sheer amount of advances they could eventually bring to road-going supercars.