How This Sustainable Alternative To Carbon Fiber Holds Up In A Crash Test
Carbon fiber changed the motorsport game when Formula One teams started using it to fabricate cars in the 1970s. A bunch of carbon atoms weaved together, carbon fiber is stiff, strong, and light—the perfect material from which to build competitive, aerodynamically-sensitive machines. But in an ecologically-conscious world, there might be a better option made from natural fibers that could outshine its originator.
While carbon fiber has been lauded as fairly ecologically-friendly, there are serious hiccups when it comes to recycling the material.
To start, carbon fiber has to be laid up by hand, which means that sheets are stacked together and combined with a plastic polymer resin to keep everything stuck together. And, as with many things done by hand, there are imprecisions in the process that lead to waste—in this case, that comes in the trimming process. A fair amount of carbon fiber ends up scrapped as a result.
And it's not exactly a substance that can be easily melted down and reformed to meet a desired shape. Carbon fiber can be recycled, but it generally needs to be done by a company that specializes in recycling composites.
Earlier this week, two companies—YCOM and Bcomp, a motorsport design company and a natural fiber composite company, respectively—announced that their journey to create a naturally-sourced version of carbon fiber has been moving ahead smoothly. As in, the composite they've created has already responded well in crash tests.
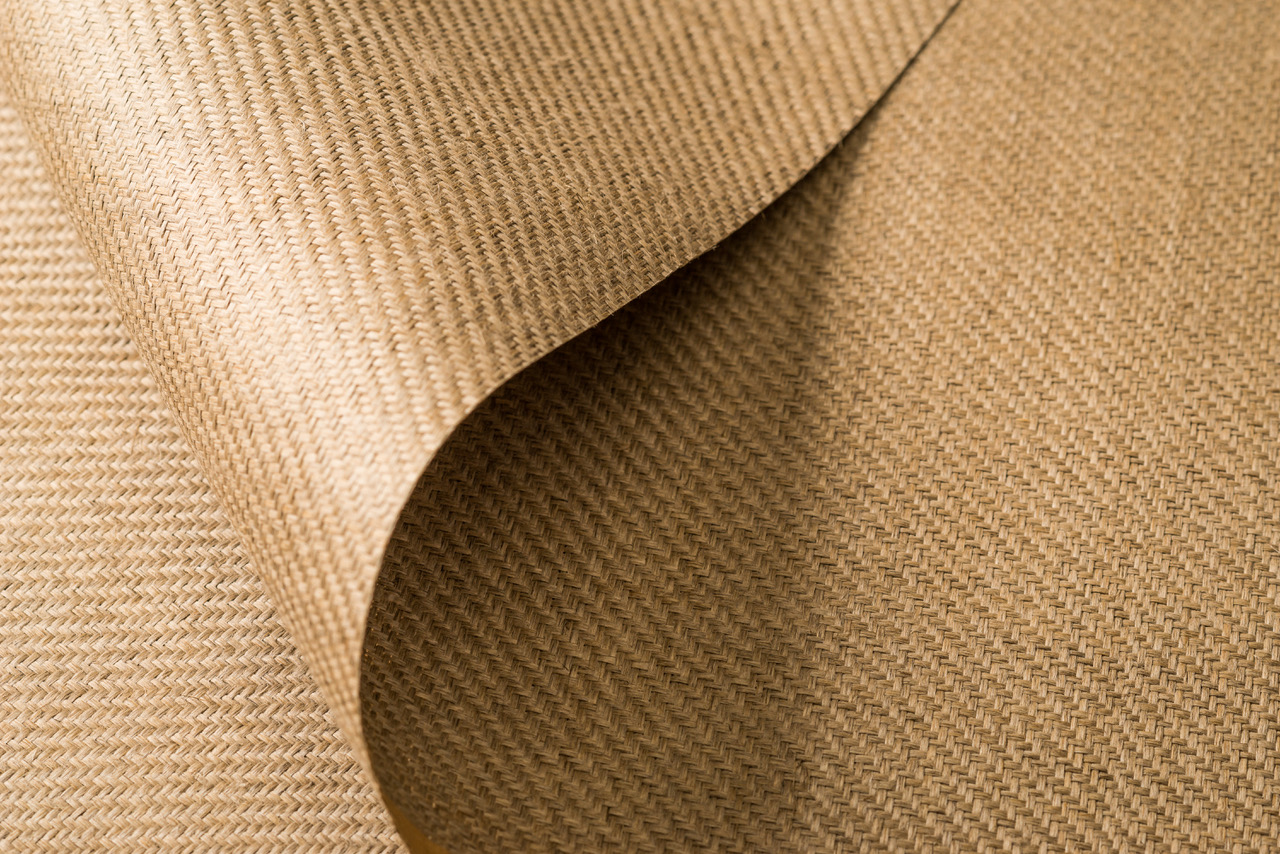
This natural carbon fiber replacement is made from something called ampliTex, which is made from flax. Flaxseed is edible and has grown in popularity as a health food supplement that aids digestion, but the fibers have also been used for ages as textile fiber. It's an adaptable plant that can grow in temperate climates around the world. It can be transformed into a smooth, strong fiber with low elasticity.
The fibers have to be reinforced, which is done through Bcomp's powerRibs technology, which does as it sounds. Also made of flax, this gridded textile is made of twisted, thick pieces of yarn that can "triple the flexural bending stiffness and thereby decrease both material use and weight, while improving vibration damping" when paired with ampliTex technology.
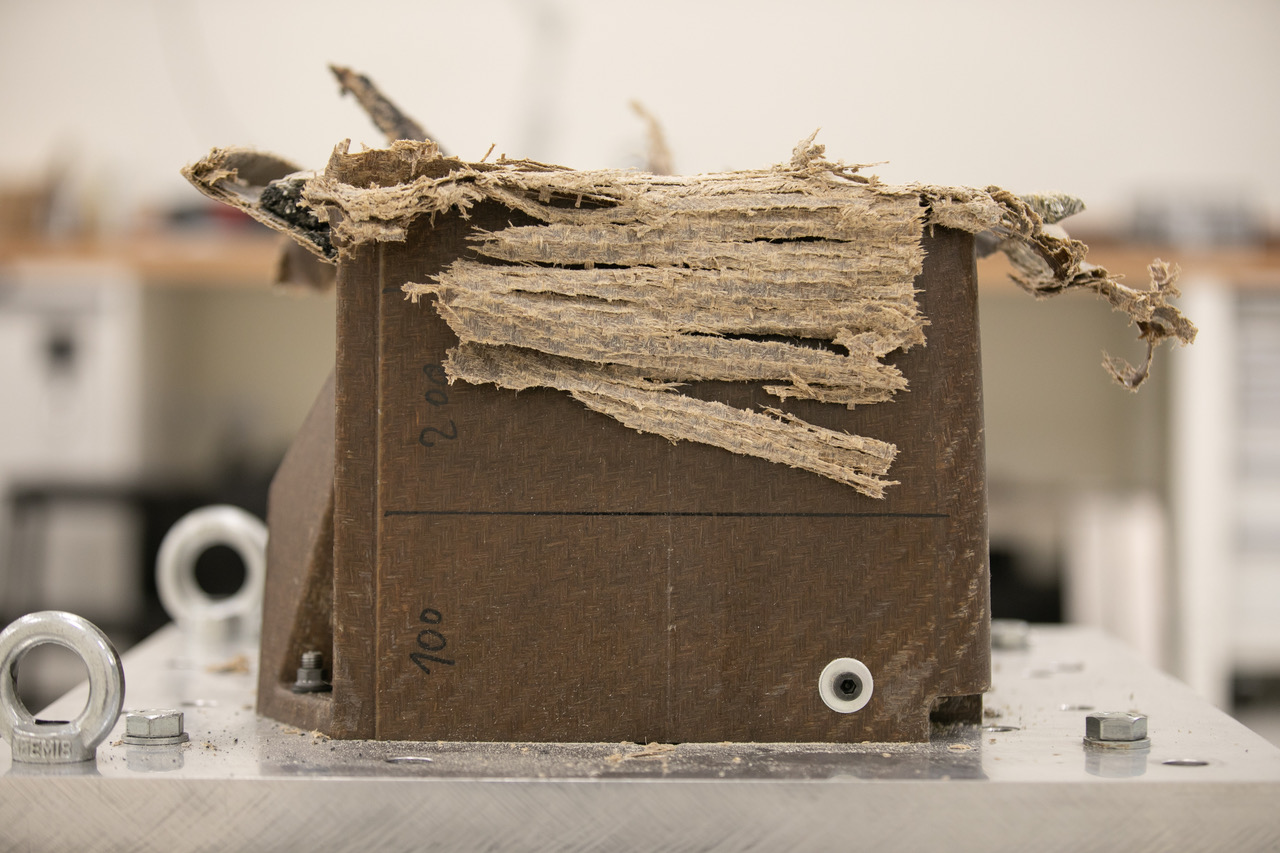
The result here are flexible, impact-dampening, lightweight, and sustainable motorsport parts that have been used in racing series like DTM and by automakers like Porsche.
It also just underwent its first FIA-approved crash test with its Front Impact Absorbing Structure, which you can watch below:
So far, the results of the tests look good. The results have been very similar to crash patterns of traditional carbon fiber structures. The main difference here is that the flax-based fibers don't splinter the same way that carbon fiber does, which is a good thing. If you've ever worked with carbon fiber, you know what a pain in the ass it can be to deal with all the pointy bits that go flying when you shave it down or break it. And, as an added benefit, all those splinters can be recycled.
Right now, the big downside is that the flax fiber has to be 40 percent heavier than its carbon fiber counterpart to achieve the same level of crash safety. That's not exactly something you want when trying to develop a lightweight machine.
But Bcomp and YCOM are have created a fascinating material on the cusp of sustainable change. Racing series like Formula One currently plan to become carbon neutral by 2050, and Formula E is always looking to push the envelope when it comes to sustainable technology. That extra weight could be engineered down, or it could be a worthy tradeoff when producing a material that emits 50 percent fewer CO2 emissions than carbon fiber.